Novel universal variable rigidity manipulator joint
A variable stiffness, robotic arm technology, applied in the directions of manipulators, manufacturing tools, joints, etc., can solve the problems of robot structure damage, destruction of operating objects, endangering operators, etc., to achieve huge application potential, increase reliability, and facilitate integration.
- Summary
- Abstract
- Description
- Claims
- Application Information
AI Technical Summary
Problems solved by technology
Method used
Image
Examples
Embodiment
[0044] Figure 6 The arc-shaped wheel disc provides a preferred structural form capable of realizing the above-mentioned functions.
[0045] Such as Figure 6 As shown, one side of the arc-shaped wheel is the hollow shaft shown in the figure, and the inner side of the shaft is an internal spline. The arc-shaped wheel is connected to the output flange through the spline and the end locking screw. hole through. The other side of the arc-shaped wheel has a three-part concave arc surface symmetrically distributed on the circumference. The arc surface adopts a Bezier curve design to provide a rolling contact surface for the roller bearing. The highest points on both sides of the concave arc surface, the arc surface Perpendicular to the face of the roulette. On the same side, a concave-convex engaging surface is provided around the middle through hole, which can cooperate with the concave-convex engaging surface of the screw nut fixing plate to limit the rotation of the arc-shape...
PUM
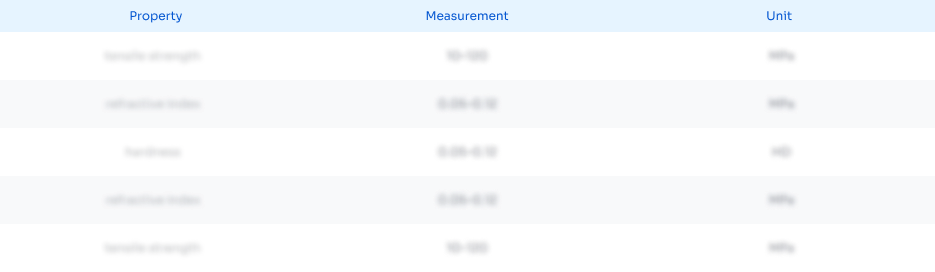
Abstract
Description
Claims
Application Information

- Generate Ideas
- Intellectual Property
- Life Sciences
- Materials
- Tech Scout
- Unparalleled Data Quality
- Higher Quality Content
- 60% Fewer Hallucinations
Browse by: Latest US Patents, China's latest patents, Technical Efficacy Thesaurus, Application Domain, Technology Topic, Popular Technical Reports.
© 2025 PatSnap. All rights reserved.Legal|Privacy policy|Modern Slavery Act Transparency Statement|Sitemap|About US| Contact US: help@patsnap.com