A Surface Treatment Process of Silica Sol Wax Model for Valve Castings
A technology of surface treatment and surface treatment device, applied in the field of foundry processing, can solve the problems of thickness deviation of wax mold, poor sand-spraying effect of wax mold, low production efficiency of wax mold, etc., and achieve the effect of increasing continuity and increasing stability.
- Summary
- Abstract
- Description
- Claims
- Application Information
AI Technical Summary
Problems solved by technology
Method used
Image
Examples
Embodiment Construction
[0036]The embodiments of the present invention will be described in detail below with reference to the accompanying drawings, but the present invention can be embodied in various ways of claims defined and covered.
[0037]Such asFigure 1 to 6As shown, a surface treatment process of a valve casting silica solve die, the surface treatment process of the valve casting silica solve wax mold, which includes a silica solve die surface treatment device including a bottom plate 1, a glue tank 2, the support table 3, the guide slip post 4, the housing sheet 5, the moving frame 6, and the locking mechanism 7, the top and rear side of the colloquil tank 2 is provided on the top of the bottom plate 1 Distributed with a support table 3, the support table 3 is mounted on the top of the outer end of the bottom plate 1, and each of the upper portion of each of the support tables 3 has a set of guiding sliding posts 4, and each of the left and right ends of each group is mounted. The sliding column pl...
PUM
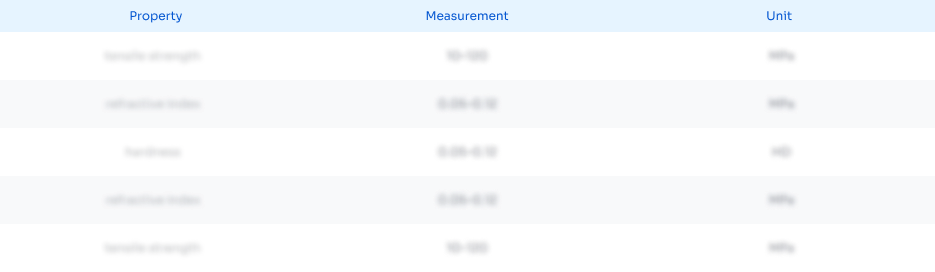
Abstract
Description
Claims
Application Information

- R&D Engineer
- R&D Manager
- IP Professional
- Industry Leading Data Capabilities
- Powerful AI technology
- Patent DNA Extraction
Browse by: Latest US Patents, China's latest patents, Technical Efficacy Thesaurus, Application Domain, Technology Topic, Popular Technical Reports.
© 2024 PatSnap. All rights reserved.Legal|Privacy policy|Modern Slavery Act Transparency Statement|Sitemap|About US| Contact US: help@patsnap.com