Self-adaptive friction energy consuming and vibration reducing device for bridge beam structure
A friction energy dissipation and vibration damping device technology, applied in bridges, bridge parts, bridge construction, etc., can solve the problems of inability to control bridge vibration energy dissipation, poor vibration reduction effect, etc., achieve good energy consumption and vibration reduction, prevent mutual Effects of collisions and falling beams
- Summary
- Abstract
- Description
- Claims
- Application Information
AI Technical Summary
Problems solved by technology
Method used
Image
Examples
Embodiment Construction
[0023] The principles and features of the present invention are described below in conjunction with the accompanying drawings, and the examples given are only used to explain the present invention, and are not intended to limit the scope of the present invention. In the following paragraphs the invention is described more specifically by way of example with reference to the accompanying drawings. Advantages and features of the present invention will be apparent from the following description and claims. It should be noted that all the drawings are in a very simplified form and use imprecise scales, and are only used to facilitate and clearly assist the purpose of illustrating the embodiments of the present invention.
[0024] Such as Figure 1-2 as shown, figure 1 It is a structural schematic diagram of an embodiment of a bridge structure self-adaptive friction energy dissipation and vibration reduction device provided by the present invention; figure 2 It is a structural ...
PUM
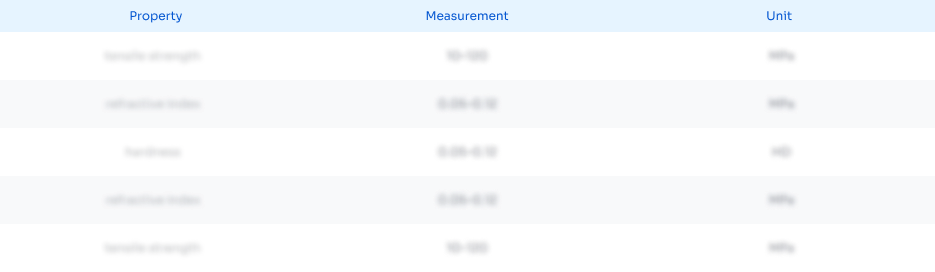
Abstract
Description
Claims
Application Information

- Generate Ideas
- Intellectual Property
- Life Sciences
- Materials
- Tech Scout
- Unparalleled Data Quality
- Higher Quality Content
- 60% Fewer Hallucinations
Browse by: Latest US Patents, China's latest patents, Technical Efficacy Thesaurus, Application Domain, Technology Topic, Popular Technical Reports.
© 2025 PatSnap. All rights reserved.Legal|Privacy policy|Modern Slavery Act Transparency Statement|Sitemap|About US| Contact US: help@patsnap.com