Industrial robot six-dimension rigidity error compensation system and compensation method thereof
An industrial robot and error compensation technology, applied in the field of robots, can solve the problems of low identification accuracy of industrial robot stiffness parameters, affecting the accuracy performance of industrial robots, and measurement data unable to fully reflect changes in industrial robot stiffness.
- Summary
- Abstract
- Description
- Claims
- Application Information
AI Technical Summary
Problems solved by technology
Method used
Image
Examples
Embodiment Construction
[0039] The specific implementation manners of the present invention will be described below in conjunction with the accompanying drawings.
[0040] Such as figure 1 As shown, the present invention provides a six-dimensional stiffness error compensation system for an industrial robot, including a load measuring device 1 and a laser tracker 2 .
[0041] The load measuring device 1 is fixed on the end of the industrial robot A, including an adapter plate 11, a six-dimensional force sensor 12, an X-axis loading device 13, a Y-axis loading device 14, a Z-axis loading device 15, a target ball 161 and a magnetic target ball base Seat 162.
[0042] The adapter plate 11 is fixedly connected with the end flange of the industrial robot A.
[0043] The six-dimensional force sensor 12 is fixed on the adapter plate 11 . The six-dimensional force sensor 12 is installed concentrically with the end flange of the industrial robot A through the adapter plate 11 .
[0044] The X-axis loading ...
PUM
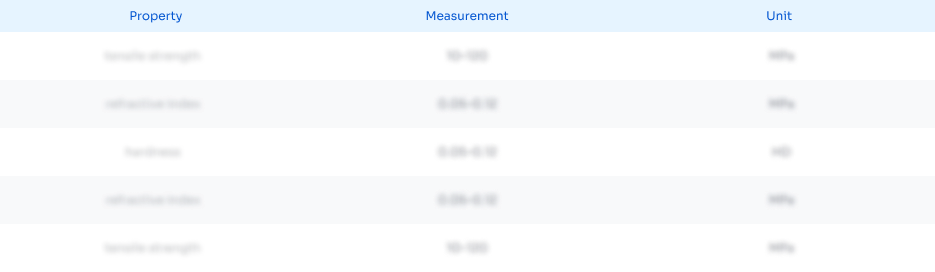
Abstract
Description
Claims
Application Information

- R&D
- Intellectual Property
- Life Sciences
- Materials
- Tech Scout
- Unparalleled Data Quality
- Higher Quality Content
- 60% Fewer Hallucinations
Browse by: Latest US Patents, China's latest patents, Technical Efficacy Thesaurus, Application Domain, Technology Topic, Popular Technical Reports.
© 2025 PatSnap. All rights reserved.Legal|Privacy policy|Modern Slavery Act Transparency Statement|Sitemap|About US| Contact US: help@patsnap.com