Tool coordinate system calibration method and calibration device for three-axis robotic arm
A technology of tool coordinate system and calibration method, applied in the field of tool coordinate system calibration, can solve the problems of difficult to guarantee accuracy, time-consuming and energy-consuming, unfavorable on-site application, etc., so as to improve the calibration accuracy, reduce the operating threshold, and achieve stable, reliable and repeatable repeatability. Effect
- Summary
- Abstract
- Description
- Claims
- Application Information
AI Technical Summary
Problems solved by technology
Method used
Image
Examples
Embodiment Construction
[0063] Example embodiments will now be described more fully with reference to the accompanying drawings. Example embodiments may, however, be embodied in many forms and should not be construed as limited to the embodiments set forth herein. Rather, these embodiments are provided so that this disclosure will be thorough and complete, and will fully convey the concept of the example embodiments to those skilled in the art. The same reference numerals denote the same or similar structures in the drawings, and thus their repeated descriptions will be omitted.
[0064] figure 1 It is a schematic flowchart of the calibration method of the tool coordinate system of the three-axis manipulator of the present invention. figure 2 It is a schematic diagram of the tool coordinate system calibration device of the three-axis mechanical arm of the present invention. like figure 1 and 2 As shown, the present invention provides a method for calibrating the tool coordinate system of a thre...
PUM
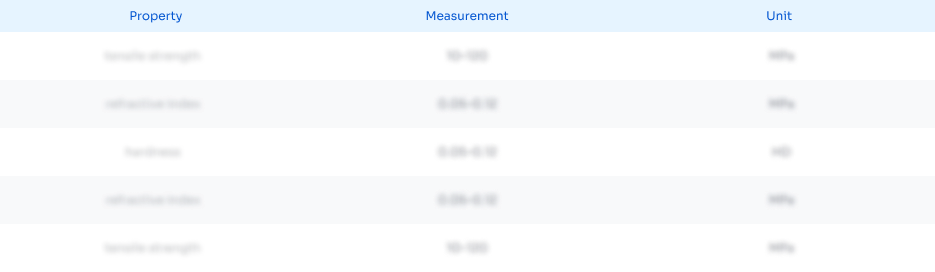
Abstract
Description
Claims
Application Information

- Generate Ideas
- Intellectual Property
- Life Sciences
- Materials
- Tech Scout
- Unparalleled Data Quality
- Higher Quality Content
- 60% Fewer Hallucinations
Browse by: Latest US Patents, China's latest patents, Technical Efficacy Thesaurus, Application Domain, Technology Topic, Popular Technical Reports.
© 2025 PatSnap. All rights reserved.Legal|Privacy policy|Modern Slavery Act Transparency Statement|Sitemap|About US| Contact US: help@patsnap.com