A tinning welding method for junction box
A welding method and tin welding technology are applied in the field of tinning and welding of junction boxes, which can solve the problems of waste of tin wire and inability to guarantee the quality of welding and welding, and achieve the effect of ensuring the quality of welding and avoiding waste.
- Summary
- Abstract
- Description
- Claims
- Application Information
AI Technical Summary
Problems solved by technology
Method used
Image
Examples
Embodiment Construction
[0027] The technical solution of the present invention will be further described below in conjunction with the accompanying drawings.
[0028] This embodiment relates to the improvement of the existing tin welding method. The improved welding method not only does not cause the waste of tin wire, but also can pre-detect the welding quality of the solder joint after the welding is completed, which greatly improves the soldering quality. work efficiency.
[0029] Specifically, the welding method of this embodiment is realized by welding equipment, see figure 1 As shown, the welding equipment includes a welding machine 1, a machine head 2, a welding head 3, a tinning mechanism 4 and an image mechanism 5, where the welding machine 1 is a DC inverter welding machine or an AC welding machine, which can provide 0-10V, The power supply of 0-3000A can make the welding head 3 heat up rapidly. The above welding methods specifically include:
[0030] (1) Move the welding head 3 of the w...
PUM
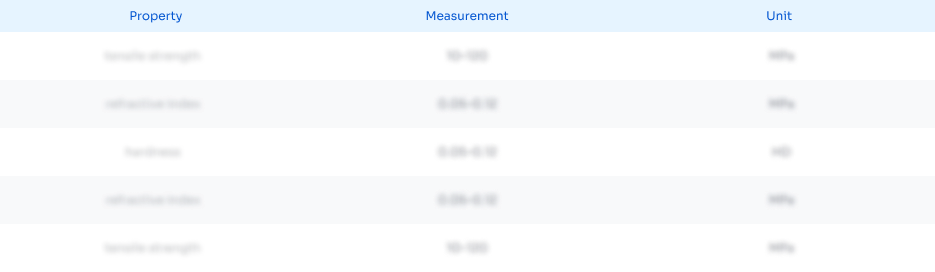
Abstract
Description
Claims
Application Information

- Generate Ideas
- Intellectual Property
- Life Sciences
- Materials
- Tech Scout
- Unparalleled Data Quality
- Higher Quality Content
- 60% Fewer Hallucinations
Browse by: Latest US Patents, China's latest patents, Technical Efficacy Thesaurus, Application Domain, Technology Topic, Popular Technical Reports.
© 2025 PatSnap. All rights reserved.Legal|Privacy policy|Modern Slavery Act Transparency Statement|Sitemap|About US| Contact US: help@patsnap.com