Workpiece spacing adjusting device
A technology for adjusting devices and spacing, applied in metal processing, manufacturing tools, metal processing equipment, etc., can solve the problems of high manufacturing and maintenance costs, complex mechanical structure, etc., and achieve low manufacturing and maintenance costs, simple structure, and high precision Effect
- Summary
- Abstract
- Description
- Claims
- Application Information
AI Technical Summary
Problems solved by technology
Method used
Image
Examples
Embodiment 1
[0045] Embodiment 1 The workpiece spacing adjustment device completes a work cycle according to the following 9 steps, and the process is as follows:
[0046] Such as figure 1 , the device is in the initial state, the piston rods of the cylinders 21, 31 are in the limit position of retraction, the driving slider 23 and the driven slider 24, and the driven sliders 24, 24' are close to each other and are in the initial position, The gripper 32 is held high with the device as a whole. The movable end 252,252' of each connecting rod 25,25' is in contact with the inner surface of the left end of the movable card slot 242,242' of the connected driven slider 24,24';
[0047] Such as figure 2 , the cylinder piston rod 311 stretches out to the limit position, the small frame 1 descends, and the holder 32 moves down to the low position along with the device;
[0048] Such as image 3 , the winding 4 whose spacing is to be adjusted is placed in the low position in advance, and the c...
PUM
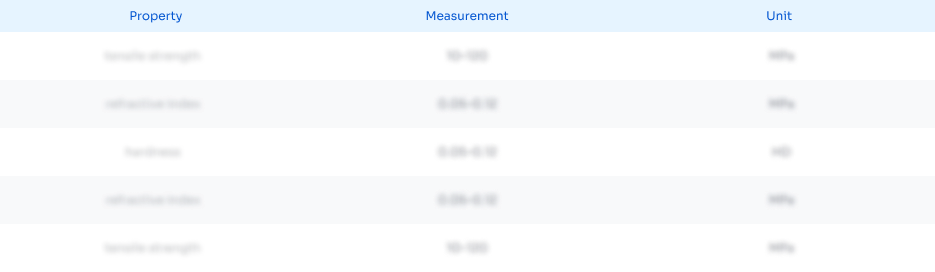
Abstract
Description
Claims
Application Information

- R&D
- Intellectual Property
- Life Sciences
- Materials
- Tech Scout
- Unparalleled Data Quality
- Higher Quality Content
- 60% Fewer Hallucinations
Browse by: Latest US Patents, China's latest patents, Technical Efficacy Thesaurus, Application Domain, Technology Topic, Popular Technical Reports.
© 2025 PatSnap. All rights reserved.Legal|Privacy policy|Modern Slavery Act Transparency Statement|Sitemap|About US| Contact US: help@patsnap.com