Loading device and method for asymmetric cyclic load of tested piece
A cyclic load and loading device technology, applied in measuring devices, using repetitive force/pulsation force to test the strength of materials, instruments, etc. The effect of reducing trial costs
- Summary
- Abstract
- Description
- Claims
- Application Information
AI Technical Summary
Problems solved by technology
Method used
Image
Examples
Embodiment Construction
[0035] like figure 1 , figure 2 As shown, it includes connecting column 1, upper specimen clamping end 2, upper catenary transition section 3, middle section 4, lower catenary transition section 5, lower specimen clamping end 6 and specimen mounting hole 7, Wherein the connecting column 1 is connected with the top of the clamping end 2 of the upper test piece, the clamping end 2 of the upper test piece is connected to the upper catenary transition section 3, and the upper catenary transition section 3 is connected to the middle section 4. The bottom of the section 4 is connected to the lower catenary transition section 5;
[0036] The connecting column 1, the upper specimen clamping end 2, the upper catenary transition section 3, the middle section 4, the lower catenary transition section 5, and the lower specimen clamping end 6 are coaxial to ensure that the mechanical vibration is only along the Longitudinal transmission to avoid the occurrence of lateral vibration;
[0...
PUM
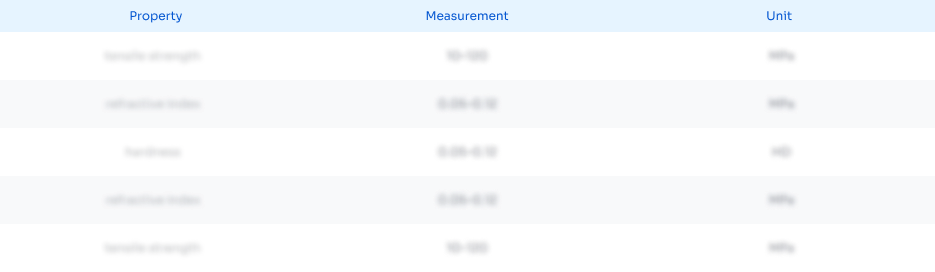
Abstract
Description
Claims
Application Information

- R&D Engineer
- R&D Manager
- IP Professional
- Industry Leading Data Capabilities
- Powerful AI technology
- Patent DNA Extraction
Browse by: Latest US Patents, China's latest patents, Technical Efficacy Thesaurus, Application Domain, Technology Topic, Popular Technical Reports.
© 2024 PatSnap. All rights reserved.Legal|Privacy policy|Modern Slavery Act Transparency Statement|Sitemap|About US| Contact US: help@patsnap.com