Autonomous calibration method of MARG sensor based on MEMS
A calibration method and sensor technology, applied in the field of inertial navigation system, can solve the problems of great influence of attitude measurement accuracy, weak magnetic induction intensity, low accuracy of MEMS sensor, etc., to achieve self-calibration, mature theoretical research, strong recognition and practicability Effect
- Summary
- Abstract
- Description
- Claims
- Application Information
AI Technical Summary
Problems solved by technology
Method used
Image
Examples
Embodiment Construction
[0015] In order to make the technical means, creative features, goals and effects achieved by the present invention easy to understand, the present invention will be further described below in conjunction with specific embodiments.
[0016] figure 1 Shown is a schematic flowchart of a three-step auxiliary calibration method for a MEMS-based MARG sensor provided by an embodiment of the present invention.
[0017] Such as figure 1 As shown, the three-step auxiliary calibration method of the MEMS-based MARG sensor provided by the embodiment of the present invention includes applying the ellipsoid fitting method to calibrate the three-axis accelerometer, applying the dot product invariant method to calibrate the three-axis magnetometer and applying The cross-product calibration method is used to calibrate the three-axis gyroscope. Specifically, the three-step auxiliary calibration method of the MEMS-based MARG sensor provided by the embodiment of the present invention includes t...
PUM
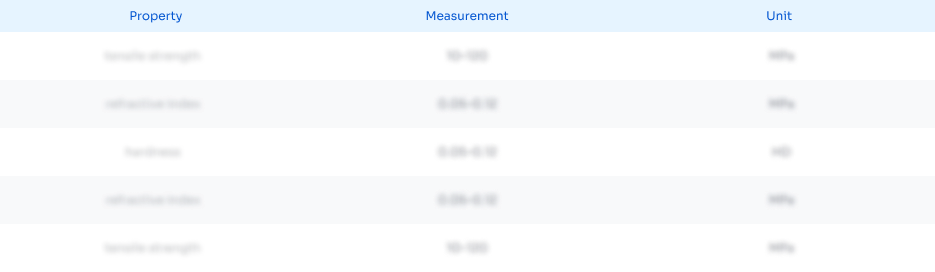
Abstract
Description
Claims
Application Information

- R&D
- Intellectual Property
- Life Sciences
- Materials
- Tech Scout
- Unparalleled Data Quality
- Higher Quality Content
- 60% Fewer Hallucinations
Browse by: Latest US Patents, China's latest patents, Technical Efficacy Thesaurus, Application Domain, Technology Topic, Popular Technical Reports.
© 2025 PatSnap. All rights reserved.Legal|Privacy policy|Modern Slavery Act Transparency Statement|Sitemap|About US| Contact US: help@patsnap.com