Surface coating process of aluminum alloy welding wire
A technology of aluminum alloy welding wire and surface coating, which is applied to the device for coating liquid on the surface, coating, insulating conductor/cable, etc. It can solve the complex coating process, uneven coating, and difficult to control coating thickness. and other problems, to achieve the effect of simple and clear operation process
- Summary
- Abstract
- Description
- Claims
- Application Information
AI Technical Summary
Problems solved by technology
Method used
Image
Examples
Embodiment 1
[0023] A process for coating the surface of an aluminum alloy welding wire, comprising the steps of:
[0024] Step (1), coating equipment commissioning and parameter setting: before starting the coating equipment, set the output oil volume and pump speed;
[0025] Step (2), coating oil heating: heating the coating oil temperature to 30°C;
[0026] Step (3), start coating: pass the clean welding wire through the coating chamber of the coating equipment, adjust the voltage of electrostatic coating and the coating speed of welding wire, and then carry out coating;
[0027] Step (4), winding: the coated welding wire is drawn into the wire take-up machine.
Embodiment 2
[0029] A process for coating the surface of an aluminum alloy welding wire, comprising the steps of:
[0030] Step (1), coating equipment debugging and parameter setting: before starting the coating equipment, set the output oil volume and pump speed; the output oil volume is controlled at 250ml / min, and the pump speed is controlled at 1200rpm;
[0031] Step (2), coating oil heating: heating the coating oil temperature to 40°C;
[0032] Step (3), start coating: pass the clean welding wire through the coating chamber of the coating equipment, adjust the voltage of electrostatic coating and the coating speed of welding wire, and then carry out coating; the coating method adopts high-voltage electrostatic coating, The coating voltage is 30Kv, the belt speed is 100m / s; the coating amount of the coating layer is 0.2g / m 2 ;
[0033] Step (4), winding: the coated welding wire is pulled into the wire take-up machine; the speed of the wire take-up is consistent with the speed of coat...
Embodiment 3
[0035] A process for coating the surface of an aluminum alloy welding wire, comprising the steps of:
[0036] Step (1), coating equipment debugging and parameter setting: before starting the coating equipment, set the output oil volume and pump speed; the output oil volume is controlled at 350ml / min, and the pump speed is controlled at 1800rpm;
[0037] Step (2), coating oil heating: heating the coating oil temperature to 60°C;
[0038] Step (3), start coating: pass the clean welding wire through the coating chamber of the coating equipment, adjust the voltage of electrostatic coating and the coating speed of welding wire, and then carry out coating; the coating method adopts high-voltage electrostatic coating, The coating voltage is 90Kv, the belt speed is 400m / s; the coating amount of the coating layer is 0.5g / m 2 ;
[0039] Step (4), winding: the coated welding wire is pulled into the wire take-up machine; the speed of the wire take-up is consistent with the speed of coat...
PUM
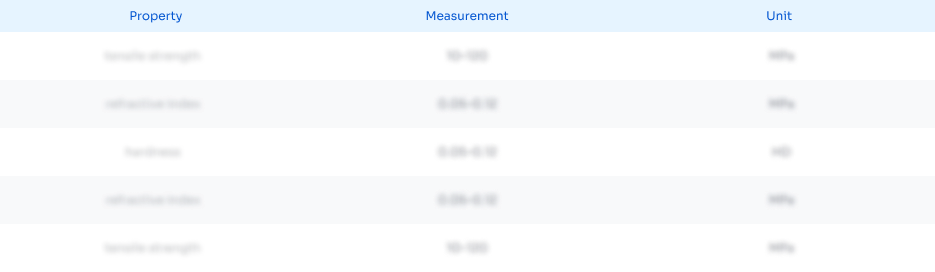
Abstract
Description
Claims
Application Information

- Generate Ideas
- Intellectual Property
- Life Sciences
- Materials
- Tech Scout
- Unparalleled Data Quality
- Higher Quality Content
- 60% Fewer Hallucinations
Browse by: Latest US Patents, China's latest patents, Technical Efficacy Thesaurus, Application Domain, Technology Topic, Popular Technical Reports.
© 2025 PatSnap. All rights reserved.Legal|Privacy policy|Modern Slavery Act Transparency Statement|Sitemap|About US| Contact US: help@patsnap.com