Field calibration method of engineering structure vibration acceleration monitoring equipment
A vibration acceleration and on-site calibration technology, which is applied in the testing/calibration of speed/acceleration/shock measurement equipment, speed/acceleration/shock measurement, and measurement devices, etc., which can solve the problem that the real-time performance of the monitoring system cannot be guaranteed and the monitoring is terminated for a long time Problems such as data and interference with the normal operation of the platform, achieve the effect of fast speed, easy operation, and strong adaptability on site
- Summary
- Abstract
- Description
- Claims
- Application Information
AI Technical Summary
Problems solved by technology
Method used
Image
Examples
Embodiment Construction
[0021] The present invention will be described below in conjunction with the accompanying drawings and embodiments. Figure 1-3 The example of the gravity pendulum device provided for the inventive method is to meet the basic requirement that the measurement value of the reference system sensor has the same acceleration input as the sensor to be calibrated when the acceleration sensor is calibrated on site, that is, the gravity pendulum device has a stable support base And real-time adjustment of the angle limit mechanism.
[0022] Below in conjunction with this example, the specific implementation is described: the gravity pendulum device of the on-site calibration of the acceleration sensor is composed of a gravity pendulum 1, a fixed bracket 2, a standard acceleration sensor 3, a sensor calibration calibration system 4, a movable pin shaft 5, and an angular positioning The pin shaft 6 is composed of the weight pendulum 1 connected with the weight hammer 7; the end of the fi...
PUM
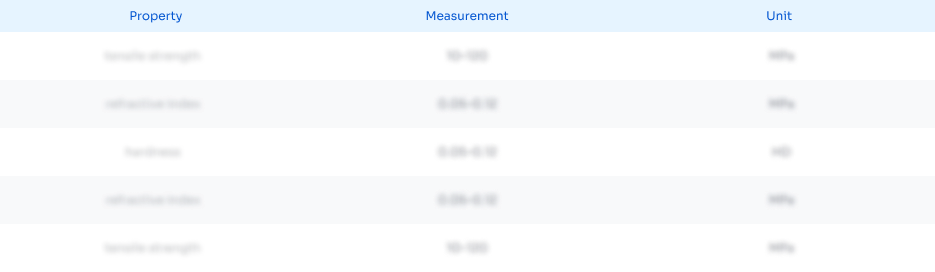
Abstract
Description
Claims
Application Information

- R&D
- Intellectual Property
- Life Sciences
- Materials
- Tech Scout
- Unparalleled Data Quality
- Higher Quality Content
- 60% Fewer Hallucinations
Browse by: Latest US Patents, China's latest patents, Technical Efficacy Thesaurus, Application Domain, Technology Topic, Popular Technical Reports.
© 2025 PatSnap. All rights reserved.Legal|Privacy policy|Modern Slavery Act Transparency Statement|Sitemap|About US| Contact US: help@patsnap.com