Programming system for hub deburring robot
A programming system and robot technology, applied in the field of wheel hub deburring robot programming system, can solve the problems of taking up the working time of industrial robots, relying on processing quality, and low efficiency, so as to achieve accurate robot trajectory, low cost, and ensure stability Effect
- Summary
- Abstract
- Description
- Claims
- Application Information
AI Technical Summary
Problems solved by technology
Method used
Image
Examples
Embodiment 1
[0016] according to figure 1 As shown, this embodiment provides a programming system for a hub deburring robot, including a model processing module, a user interaction module, a deburring path generation module and an offline program generation module, and the model processing module reads the wheel hub to be processed The 3D model of the wheel hub is selected in an interactive way through the user interaction module and the deburring path generation module, and the processing path is discretized; by selecting the discretized key points, it is used as Feature points, add the attitude information of the key points according to the hub deburring process parameters, select the linear or arc transition mode between each key point, and add the speed and acceleration parameters of the robot movement; then according to the three-dimensional coordinate information of the key points and their For related information, the program that the robot can run directly is generated through the ...
Embodiment 2
[0025] like figure 2 As shown, the present embodiment provides a programming system for a hub deburring robot, comprising the following steps:
[0026] Step 1: Use the model processing module to import the hub model;
[0027] Step 2: Select the deburring processing path in an interactive way;
[0028] Step 3: The discrete processing path of the model processing module is a point;
[0029] Step 4: Select key points interactively, and set attitude information in the system interface;
[0030] Step 5: Set the robot's movement mode, speed, acceleration and other related information;
[0031] Step 6: generate a robot program by an offline program generation module;
[0032] Step 7: Carry out the actual wheel hub deburring test, if the requirements are met, proceed to the follow-up; if not, re-select key points and set relevant information.
[0033] The generation of the processing path is controlled by the way the user selects key points, and the program is generated by selec...
PUM
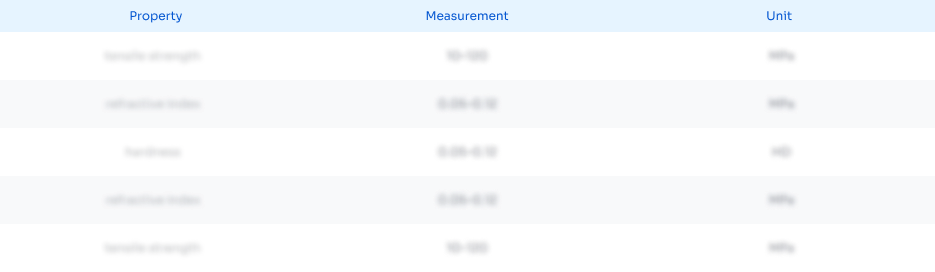
Abstract
Description
Claims
Application Information

- Generate Ideas
- Intellectual Property
- Life Sciences
- Materials
- Tech Scout
- Unparalleled Data Quality
- Higher Quality Content
- 60% Fewer Hallucinations
Browse by: Latest US Patents, China's latest patents, Technical Efficacy Thesaurus, Application Domain, Technology Topic, Popular Technical Reports.
© 2025 PatSnap. All rights reserved.Legal|Privacy policy|Modern Slavery Act Transparency Statement|Sitemap|About US| Contact US: help@patsnap.com