Industrial robot stop motion trajectory planning method
A technology of industrial robots and motion trajectories, applied in manipulators, manufacturing tools, program-controlled manipulators, etc., can solve problems such as lagging trajectory interpolation speed, achieve the effects of small calculation, simple model, and improved speed and timeliness
- Summary
- Abstract
- Description
- Claims
- Application Information
AI Technical Summary
Problems solved by technology
Method used
Image
Examples
Embodiment
[0038] Taking the joint motion of an industrial robot as an example, the method of the present invention is used to plan the stop motion trajectory of the industrial robot, and the specific steps are as follows:
[0039] Step 1. Create a buffer to store the trajectory interpolation output information:
[0040] The size of the cache is 25. The joint position output in each interpolation cycle during normal operation is the joint data recorded at the first position of the cache, and the joint data recorded at the 25th position is the joint data corresponding to the current trajectory interpolation. Each position data is shifted one bit forward.
[0041] Step 2. When receiving the stop command, plan to stop the cache segment data:
[0042] Step 2.1. Add time information to the data in the cache. The time difference between adjacent cache positions is the interpolation period Tc=0.004s, and the time corresponding to the 1st, 2, 3...N+1 positions of the cache is 0, 0.004, 0.008......
PUM
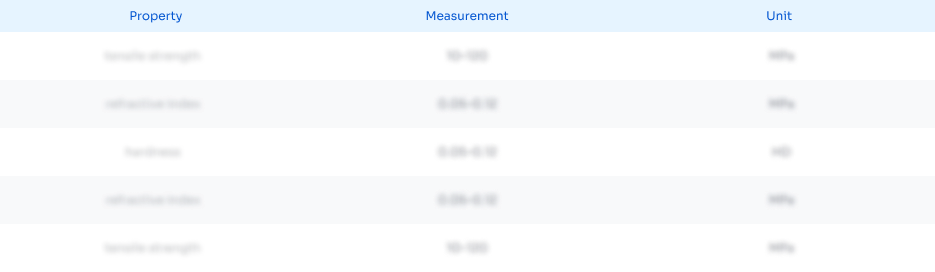
Abstract
Description
Claims
Application Information

- R&D Engineer
- R&D Manager
- IP Professional
- Industry Leading Data Capabilities
- Powerful AI technology
- Patent DNA Extraction
Browse by: Latest US Patents, China's latest patents, Technical Efficacy Thesaurus, Application Domain, Technology Topic, Popular Technical Reports.
© 2024 PatSnap. All rights reserved.Legal|Privacy policy|Modern Slavery Act Transparency Statement|Sitemap|About US| Contact US: help@patsnap.com