Stepless speed changing device with speed adjusting component arranged inside
A continuously variable transmission device and speed regulation technology, which is applied in the direction of control devices, transmission devices, vehicle components, etc., can solve problems such as structural size and weight that cannot be solved, and achieve the effect of optimizing the efficiency of all working conditions
- Summary
- Abstract
- Description
- Claims
- Application Information
AI Technical Summary
Problems solved by technology
Method used
Image
Examples
Embodiment 1
[0059] Further explanation in conjunction with the accompanying drawings: In this embodiment, there are two power coupling shafts: power coupling shaft I and power coupling shaft II, and they are coaxial with the cone-disc shaft system I and the cone-disk shaft system II respectively, such as Figure 1-4 The continuously variable transmission device built in the speed regulating components shown includes the cone shaft system I 001, the cone shaft system II 002, the speed control shaft system 18, the power coupling shaft I 1 and the power coupling shaft II17.
[0060] In this embodiment, the power coupling axis I 1 is coaxial with the cone shaft system I, and the power coupling shaft II 17 is coaxial with the cone shaft system I.
[0061] Such as Figure 2-4 As shown, the speed regulating shaft system is arranged between the two cone-disk shaft systems and in the cross-section of the three shaft systems, the three shafts are arranged in a triangle. The cone-disk shaft system I...
Embodiment 2
[0092] Such as Figure 5 As shown, the difference from Embodiment 1 is that the power coupling shaft of this embodiment is not coaxial with the cone-disc shaft system I and the cone-disk shaft system II, and the pressurization mechanism of this embodiment includes a set of pressurization springs 24. One end of the pressure spring 24 is pressed on the fixed cone 10, and the other end is pressed on the spring seat 6.
Embodiment approach
[0094] Dynamically coupled axes can be set in the following different ways:
[0095] Power coupling axis 1 is connected to the spring seat:
[0096] The power coupling shaft 1 is not coaxial with the speed regulating screw 21, and the power coupling shaft 1 and the spring seat are connected through gear meshing or a chain. The chain is preferably a toothed chain, preferably a toothed silent chain.
[0097] The power coupling shaft 1 is coaxial with the speed regulating screw 21, and the power coupling shaft 1 is connected to the spring seat 6 through a spline.
[0098] The power coupling shaft 1 is coaxial with the speed regulating screw 21. The power coupling shaft 1 and the spring seat 6 are connected through the axially slidable spline sleeve 5. The spline sleeve 5 can slide axially to different positions, and the power coupling can be coupled or decoupled. Power between shaft 1 and spring seat 6. The splined sleeve 5 is preferably driven by an electric motor.
[0099] T...
PUM
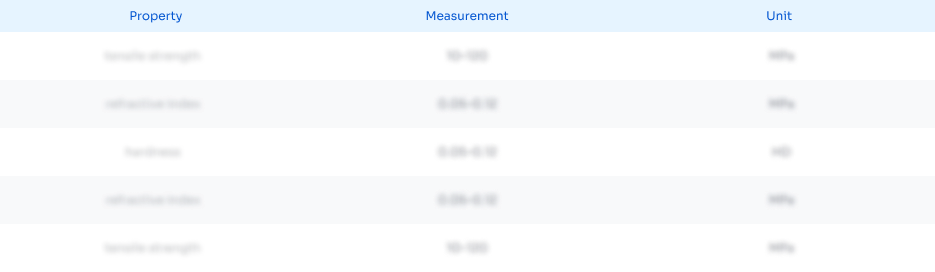
Abstract
Description
Claims
Application Information

- R&D
- Intellectual Property
- Life Sciences
- Materials
- Tech Scout
- Unparalleled Data Quality
- Higher Quality Content
- 60% Fewer Hallucinations
Browse by: Latest US Patents, China's latest patents, Technical Efficacy Thesaurus, Application Domain, Technology Topic, Popular Technical Reports.
© 2025 PatSnap. All rights reserved.Legal|Privacy policy|Modern Slavery Act Transparency Statement|Sitemap|About US| Contact US: help@patsnap.com