Three-dimensional configuration splicing method for large component based on laser vision sensing
A large-scale component and visual sensing technology, applied in the direction of optical devices, measuring devices, instruments, etc., can solve the problems of difficult to achieve online measurement, poor anti-interference ability, heavy workload, etc., achieve fast speed, small stitching error, good accessibility
- Summary
- Abstract
- Description
- Claims
- Application Information
AI Technical Summary
Problems solved by technology
Method used
Image
Examples
specific Embodiment approach 1
[0047] Specific embodiment one: a kind of large component three-dimensional configuration splicing method based on laser vision sensing of the present embodiment, it is carried out according to the following steps:
[0048] Step 1: Before measuring the contour of the profile, first calibrate the laser vision sensor, and restore the two-dimensional pixel image of the computer to the earth coordinates;
[0049] Step 2: Rigidly fix the laser vision sensor and the motion system to ensure that the sensor is always in the common working range during the motion process;
[0050] Step 3: Establish communication between the laser vision sensor and the PC controller, set sensor parameters, and set motion system parameters;
[0051] Step 4: The image scanning unit scans the profile image of the workpiece to be tested, and each scan obtains an array of 512 pixel points, the abscissa ranges from 0 to 511, the ordinate ranges from 0 to 1023, and the point array is in the abscissa Arranging...
specific Embodiment approach 2
[0070] Embodiment 2: This embodiment differs from Embodiment 1 in that the filtering algorithm is mean filtering, median filtering, Hamming filtering, quadratic filtering or bell-shaped filtering.
[0071] Others are the same as in the first embodiment.
specific Embodiment approach 3
[0072] Embodiment 3: The difference between this embodiment and Embodiment 1 is that the laser vision sensor is a linear laser sensor. Others are the same as in the first embodiment.
PUM
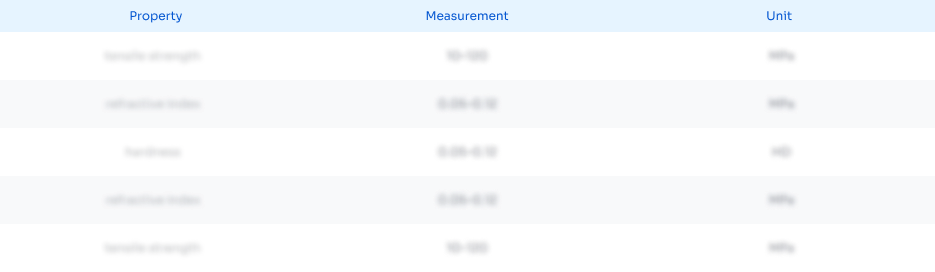
Abstract
Description
Claims
Application Information

- R&D
- Intellectual Property
- Life Sciences
- Materials
- Tech Scout
- Unparalleled Data Quality
- Higher Quality Content
- 60% Fewer Hallucinations
Browse by: Latest US Patents, China's latest patents, Technical Efficacy Thesaurus, Application Domain, Technology Topic, Popular Technical Reports.
© 2025 PatSnap. All rights reserved.Legal|Privacy policy|Modern Slavery Act Transparency Statement|Sitemap|About US| Contact US: help@patsnap.com