An automatic calibration method of robot hand-eye relationship based on incremental compensation
A robot hand and automatic calibration technology, which is applied to manipulators, program-controlled manipulators, instruments, etc., can solve the problems of accuracy affecting calibration accuracy, complicated operation, limited application, etc., to improve calibration efficiency, simplify calibration procedures, and improve calibration. The effect of efficiency
- Summary
- Abstract
- Description
- Claims
- Application Information
AI Technical Summary
Problems solved by technology
Method used
Image
Examples
Embodiment Construction
[0028] Preferred embodiments of the present disclosure will be described in more detail below with reference to the accompanying drawings. Although preferred embodiments of the present disclosure are shown in the drawings, it should be understood that the present disclosure can be embodied in various forms and should not be limited to the embodiments set forth herein. Rather, these embodiments are provided so that this disclosure will be thorough and complete, and will fully convey the scope of the disclosure to those skilled in the art.
[0029] attached figure 1 The flow chart of the automatic calibration method for robot hand-eye relationship based on incremental compensation according to an exemplary embodiment is given in . As shown in the figure, an exemplary automatic calibration method for hand-eye relationship includes the following steps:
[0030] Guide the end of the robotic arm to the appropriate calibration origin, collect the image of the calibration object on ...
PUM
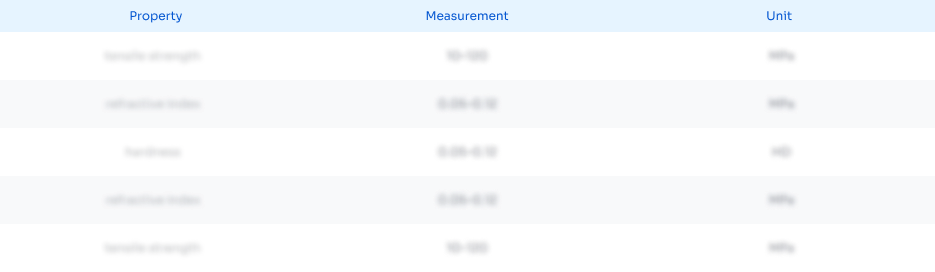
Abstract
Description
Claims
Application Information

- R&D
- Intellectual Property
- Life Sciences
- Materials
- Tech Scout
- Unparalleled Data Quality
- Higher Quality Content
- 60% Fewer Hallucinations
Browse by: Latest US Patents, China's latest patents, Technical Efficacy Thesaurus, Application Domain, Technology Topic, Popular Technical Reports.
© 2025 PatSnap. All rights reserved.Legal|Privacy policy|Modern Slavery Act Transparency Statement|Sitemap|About US| Contact US: help@patsnap.com