Kinematic calibration method for parallel machining equipment
A technology of processing equipment and calibration methods, applied in the field of kinematics calibration, can solve the problems of failing to analyze the influence of measurement methods in depth, error modeling and parameter identification method finalization, etc.
- Summary
- Abstract
- Description
- Claims
- Application Information
AI Technical Summary
Problems solved by technology
Method used
Image
Examples
Embodiment approach 1
[0077] Such as image 3 As shown, the motion diagram when the parallel processing equipment is a five-axis parallel processing robot. Among them, branch 1 is U P RR configuration, where U is a universal joint, P is a linear pair, R is a rotary joint, and R is an active joint), branch chains 2 to 5 are U P RU configuration. Node B i and A i (i=1...5) are respectively the center point of the U pair connecting the branch chain i with the frame and the moving platform. Node B 1 , B 2 and B 3 Evenly distributed on a certain circle, the radius of the circle is r 1 , with center O and radius OB 1 , OB 2 and OB 3 The angle between them is denoted as γ. Establish the robot coordinate system {rt:O-XYZ} at the center O of the circle, and the reverse extension line of the X axis passes through the node B 1 , the Z axis is perpendicular to the circle. Node B 4 and B 5 Symmetrically distributed on both sides of the surface XOZ, while distributed in a certain radius r 2 , th...
Embodiment approach 2
[0124] From the analysis in Embodiment 1, it can be seen that the error model of the five-axis parallel robot is:
[0125]
[0126] It is known that for a five-axis parallel processing robot, the spatial pose of the spindle can be uniquely determined by three points that are relatively fixed and not collinear. Therefore, in this embodiment, the following method is used to measure the position of the three points: the auxiliary workpiece and the spindle tool handle are clamped and then fixed, and the target ball is sequentially detected and placed on the target seat C 1 、C 2 、C 3 The location coordinates at time. At the same time, in order to unify the measurement results in the robot coordinate system, an auxiliary workpiece coordinate system {at:o * -x * the y * z *}, where the origin o * with point C 1 Coincident, x * Axis points to point C 2 ,z * axis and plane C 1 C 2 C 3 vertical. Let point C i (i=1,2,3) The theoretical position coordinates in the coord...
PUM
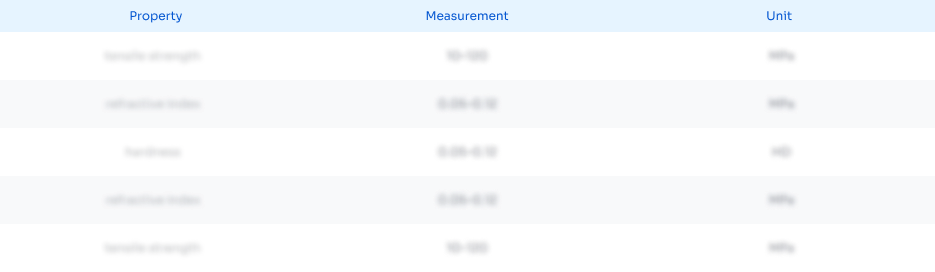
Abstract
Description
Claims
Application Information

- Generate Ideas
- Intellectual Property
- Life Sciences
- Materials
- Tech Scout
- Unparalleled Data Quality
- Higher Quality Content
- 60% Fewer Hallucinations
Browse by: Latest US Patents, China's latest patents, Technical Efficacy Thesaurus, Application Domain, Technology Topic, Popular Technical Reports.
© 2025 PatSnap. All rights reserved.Legal|Privacy policy|Modern Slavery Act Transparency Statement|Sitemap|About US| Contact US: help@patsnap.com