Kinematic calibration method for Stewart parallel robot
A technology of robot kinematics and calibration method, applied in the field of Stewart type parallel robot kinematics calibration, can solve the problems such as deviation of branch motion direction and node connection, inability to obtain accurate kinematics model, inaccurate position of connection point, etc. The effect of reducing model accuracy, strong practicability, and user-friendly interface
- Summary
- Abstract
- Description
- Claims
- Application Information
AI Technical Summary
Problems solved by technology
Method used
Image
Examples
Embodiment Construction
[0032] The present invention will be described in further detail below in conjunction with the accompanying drawings and embodiments.
[0033] The calibration method of the parallel robot of the present invention comprises four parts: establishment of a Stewart type parallel robot kinematics model, establishment of a measurement process model, establishment of a calibration system model, and solution of a nonlinear calibration model to identify kinematic parameters.
[0034] The establishment of the kinematics model of the Stewart type parallel robot includes: the establishment of the coordinate system of the Stewart type parallel robot, the determination of the minimum parameter set to be identified, and the expression of the kinematic relationship.
[0035] like figure 1 As shown, the method for establishing the Stewart type parallel robot coordinate system is as follows:
[0036] First, the mechanism of the Stewart type parallel robot to be modeled is as follows: the robot...
PUM
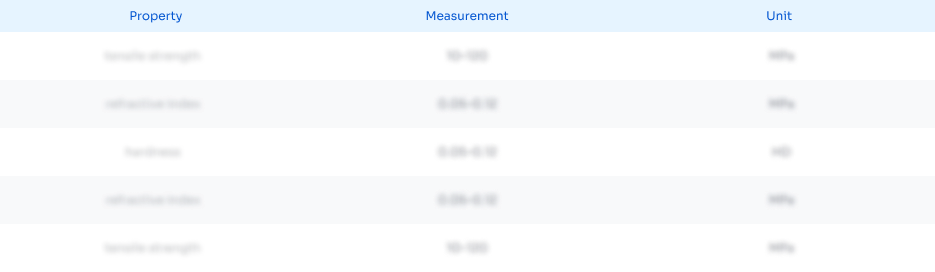
Abstract
Description
Claims
Application Information

- R&D
- Intellectual Property
- Life Sciences
- Materials
- Tech Scout
- Unparalleled Data Quality
- Higher Quality Content
- 60% Fewer Hallucinations
Browse by: Latest US Patents, China's latest patents, Technical Efficacy Thesaurus, Application Domain, Technology Topic, Popular Technical Reports.
© 2025 PatSnap. All rights reserved.Legal|Privacy policy|Modern Slavery Act Transparency Statement|Sitemap|About US| Contact US: help@patsnap.com