Heavy-duty lifting robot based on parallel wire driven mechanism
A robot and flexible cable technology, applied in the field of heavy-duty hoisting robots, can solve problems such as low efficiency, inability to realize automatic operations, assembly positioning, and difficulty in attitude adjustment, so as to reduce internal load, force, and structure. force effect
- Summary
- Abstract
- Description
- Claims
- Application Information
AI Technical Summary
Problems solved by technology
Method used
Image
Examples
Embodiment Construction
[0026] The present invention will be described in further detail below in conjunction with the accompanying drawings.
[0027] Such as figure 1 As shown, the present invention includes an upper platform 1, a lower platform 3 and six flexible cables 2, the upper platform 1 is a fixed platform, the lower platform 3 is a moving platform, and the upper platform 1 and the lower platform 3 are connected by six flexible cables 2 to form a Stewart type parallel connection Mechanism: the two ends of each flexible cable 2 are respectively connected with the upper platform 1 and the lower platform 3 to form a branch, a total of six isomorphic branches. Six fixed pulleys 6 and six motors 5 are respectively installed on the upper platform 1, and the output end of each motor 5 is connected with a reel 4, and six cross hinges 7 are installed on the lower platform 3. The upper end of the cable 2 in each branch is wound on the reel 4 driven by the motor 5 through the fixed pulley 6 installed ...
PUM
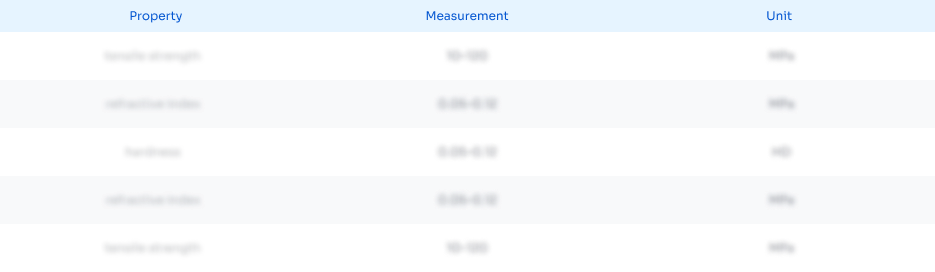
Abstract
Description
Claims
Application Information

- Generate Ideas
- Intellectual Property
- Life Sciences
- Materials
- Tech Scout
- Unparalleled Data Quality
- Higher Quality Content
- 60% Fewer Hallucinations
Browse by: Latest US Patents, China's latest patents, Technical Efficacy Thesaurus, Application Domain, Technology Topic, Popular Technical Reports.
© 2025 PatSnap. All rights reserved.Legal|Privacy policy|Modern Slavery Act Transparency Statement|Sitemap|About US| Contact US: help@patsnap.com