Pick-and-place device for microseismic sensor with strain gauge sticking structure and method of use thereof
A technology of microseismic sensor and pick-and-place device, which is applied to measurement devices, seismic signal receivers, instruments, etc., can solve the problems of unrecoverable sensors, failure to monitor hole wall strain, and extended construction period.
- Summary
- Abstract
- Description
- Claims
- Application Information
AI Technical Summary
Problems solved by technology
Method used
Image
Examples
Embodiment Construction
[0049] The present invention will be further described below in conjunction with accompanying drawing:
[0050] Such as figure 1 , figure 2 , image 3 The shown pick-and-place device for microseismic sensors with a strain gauge pasting structure includes a support wall assembly with a hollow columnar structure as a whole. The support wall assembly is formed by combining two symmetrically arranged arc-shaped plates 1 with the same structure. Such as Figure 8 , Figure 9 As shown, the inner walls of the two arc-shaped plates 1 are respectively provided with square grooves 12 inwardly, and the groove walls on both sides of the groove 12 are symmetrically provided with slide bar grooves 13, and the grooves 12 are also provided with connecting two grooves. The fixed rod 14 of the side groove wall, the fixed rod 14 is arranged on the side close to the microseismic sensor 4, the setting direction of the groove 12 and the slide rod groove 13 coincides with the axial direction of...
PUM
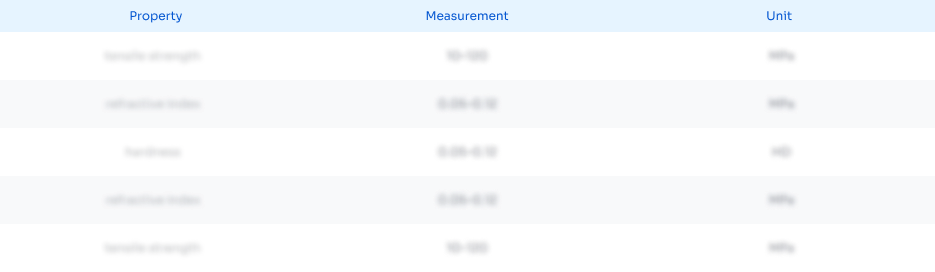
Abstract
Description
Claims
Application Information

- R&D Engineer
- R&D Manager
- IP Professional
- Industry Leading Data Capabilities
- Powerful AI technology
- Patent DNA Extraction
Browse by: Latest US Patents, China's latest patents, Technical Efficacy Thesaurus, Application Domain, Technology Topic, Popular Technical Reports.
© 2024 PatSnap. All rights reserved.Legal|Privacy policy|Modern Slavery Act Transparency Statement|Sitemap|About US| Contact US: help@patsnap.com