Cooling liquid flow monitoring method and liquid cooling electric drive system
A flow monitoring and cooling liquid technology, which is applied in liquid/fluid solid measurement, measuring flow/mass flow, electrical devices, etc., can solve the problem that the cooling liquid flow cannot be monitored, achieve high reliability, avoid dispersion, and improve Product Cost Effects
- Summary
- Abstract
- Description
- Claims
- Application Information
AI Technical Summary
Problems solved by technology
Method used
Image
Examples
Embodiment 1
[0072] Please refer to Figure 1 to Figure 4 ,in, figure 1 It is a schematic diagram of the liquid-cooled electric drive system provided in Embodiment 1 of the present invention, figure 2 It is a schematic diagram of the power module and the liquid cooling channel provided by Embodiment 1 of the present invention, image 3 It is a flow chart of the coolant flow monitoring method provided in Embodiment 1 of the present invention, Figure 4 It is a flow chart of preset rules of the coolant flow monitoring method provided in Embodiment 1 of the present invention.
[0073] Embodiment 1 of the present invention provides a coolant flow monitoring method and a liquid-cooled electric drive system. The coolant flow monitoring method is mainly used in liquid-cooled electric drive systems, such as figure 1 As shown, in an exemplary embodiment, the liquid-cooled electric drive system includes a liquid-cooled channel 10, a DC power supply 20, a control module 30, a power module 40, and...
Embodiment 2
[0090] The cooling liquid flow monitoring method and the liquid-cooled electric drive system of the second embodiment of the present invention are basically the same as those of the first embodiment, the same parts will not be described, and only the differences will be described below.
[0091] Please refer to Figure 5 , which is a flow chart of preset rules of the coolant flow monitoring method provided in Embodiment 2 of the present invention.
[0092] In the second embodiment, the setting positions of the first reference point and the second reference point are different from those in the first embodiment. Specifically, the first reference point is set in the liquid cooling channel 10, and the second reference point is set in the power module 40, such as Figure 5 As shown, the preset rules specifically include:
[0093] Step S32a: using the temperature difference measured between the first reference point and the second reference point as the second temperature differe...
Embodiment 3
[0109] In the third embodiment, both the first reference point and the second reference point are set in the power module 40. Preferably, the power module 40 includes a multi-phase power unit, and the multi-phase power unit Arranged in sequence according to the flow direction of the coolant, the first reference point is set on the power unit close to the inlet of the coolant, and the second reference point is set on the power unit close to the outlet of the coolant superior. In an exemplary embodiment, the liquid-cooled electric drive system includes a first temperature sensor and a second temperature sensor, please refer to figure 2 , the three-phase power units 41, 42, 43 of the power module 40 are arranged sequentially along the flow direction of the coolant, the NTC temperature sensor 44 is configured as a first temperature sensor, and is set as a first reference point, and the NTC temperature sensor 46 Configured as the first temperature sensor and set as the second ref...
PUM
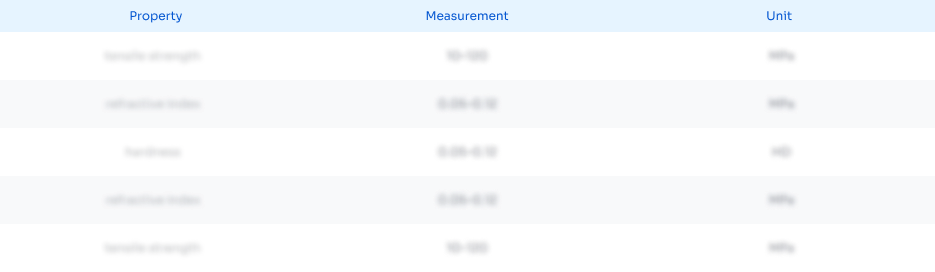
Abstract
Description
Claims
Application Information

- R&D
- Intellectual Property
- Life Sciences
- Materials
- Tech Scout
- Unparalleled Data Quality
- Higher Quality Content
- 60% Fewer Hallucinations
Browse by: Latest US Patents, China's latest patents, Technical Efficacy Thesaurus, Application Domain, Technology Topic, Popular Technical Reports.
© 2025 PatSnap. All rights reserved.Legal|Privacy policy|Modern Slavery Act Transparency Statement|Sitemap|About US| Contact US: help@patsnap.com