Self-programmable multi-shaft target shooting robot
A self-programming and robot technology, applied in the field of target shooting robots, can solve the problems of not being able to rotate at multiple angles, not being able to change the way of moving, and requiring high requirements for the use of the site, achieving powerful functions, reducing the number of purchases, and good stability.
- Summary
- Abstract
- Description
- Claims
- Application Information
AI Technical Summary
Problems solved by technology
Method used
Image
Examples
Embodiment Construction
[0020] The technical solutions of the present invention will be further described below in conjunction with the accompanying drawings and embodiments.
[0021] like figure 1 As shown, the self-programmable multi-axis target shooting robot of the present invention includes a chassis 1, two front wheels, one rear wheel or two rear wheels, which are selected according to actual load requirements. The front wheel is a brushless hub motor 4, and the two front wheels are responsible for advancing steering, and the rear wheel is a shock-absorbing universal wheel 2, which buffers and absorbs the shock of the car body. The shock-absorbing design is adopted to reduce the height of the chassis and remove the track design, while ensuring that the wading depth is 10 cm. Through the shock-absorbing device, the requirements for the ground are greatly reduced, and it can pass through gravel, steep slopes, muddy and other harsh road sections. A target seat 7 is arranged above the chassis 1, a...
PUM
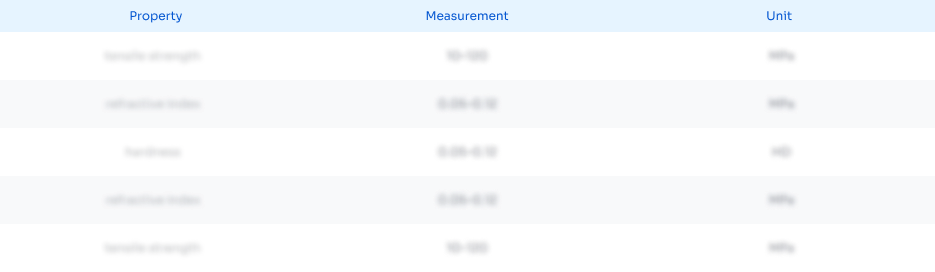
Abstract
Description
Claims
Application Information

- R&D
- Intellectual Property
- Life Sciences
- Materials
- Tech Scout
- Unparalleled Data Quality
- Higher Quality Content
- 60% Fewer Hallucinations
Browse by: Latest US Patents, China's latest patents, Technical Efficacy Thesaurus, Application Domain, Technology Topic, Popular Technical Reports.
© 2025 PatSnap. All rights reserved.Legal|Privacy policy|Modern Slavery Act Transparency Statement|Sitemap|About US| Contact US: help@patsnap.com