Annular thin-wall part forming method, forming mold and forming stamping tool
A forming method and forming mold technology, which are applied in the direction of manufacturing tools, forging/pressing/hammer devices, forging/pressing/hammering machinery, etc., can solve the problems of large forming resistance, low working life, and high energy consumption for the production of a single part. Achieve the effects of small forming resistance, improved working life and reduced production energy consumption
- Summary
- Abstract
- Description
- Claims
- Application Information
AI Technical Summary
Problems solved by technology
Method used
Image
Examples
Embodiment Construction
[0038] Below, the present invention will be further described in conjunction with the accompanying drawings and specific implementation methods. It should be noted that, under the premise of not conflicting, the various embodiments described below or the technical features can be combined arbitrarily to form new embodiments. .
[0039] A method for forming an annular thin-walled part, which is applied to a columnar blank, is characterized in that the method for forming comprises the following steps:
[0040] Material breaking steps: reference figure 1 , intercept a certain length of the initial billet segment.
[0041] Shaping steps: reference Figure 1 to Figure 3 , the upper and lower ends of the initial blank section are shaped to smooth the cut marks on the upper and lower ends of the initial blank section.
[0042] Head Upsetting Steps: Reference Figure 3 to Figure 5 , Upsetting the upper end of the initial blank section to form the head 1, so that the initial blank...
PUM
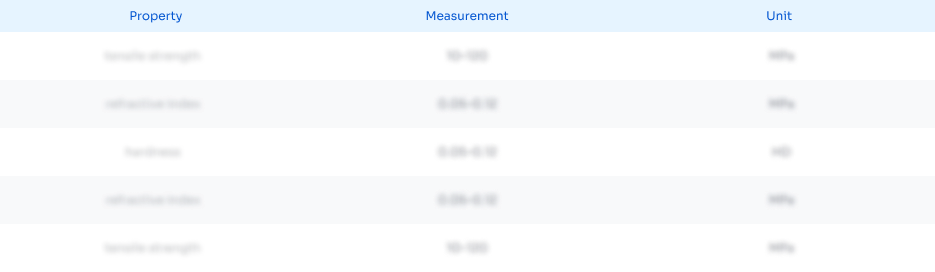
Abstract
Description
Claims
Application Information

- Generate Ideas
- Intellectual Property
- Life Sciences
- Materials
- Tech Scout
- Unparalleled Data Quality
- Higher Quality Content
- 60% Fewer Hallucinations
Browse by: Latest US Patents, China's latest patents, Technical Efficacy Thesaurus, Application Domain, Technology Topic, Popular Technical Reports.
© 2025 PatSnap. All rights reserved.Legal|Privacy policy|Modern Slavery Act Transparency Statement|Sitemap|About US| Contact US: help@patsnap.com