Combustion chamber heat protection wall structure using fuel self-suction sweat cooling
A sweat cooling and thermal protection technology, applied in combustion chambers, continuous combustion chambers, combustion methods, etc., can solve problems such as insufficient fuel heat sink, easy coking and clogging, and achieve the effects of lowering temperature, avoiding coking and clogging, and realizing recycling
- Summary
- Abstract
- Description
- Claims
- Application Information
AI Technical Summary
Problems solved by technology
Method used
Image
Examples
Embodiment 1
[0030] Such as Figure 2-6 As shown, this embodiment provides a combustion chamber heat protection wall structure that utilizes self-suction and sweating of fuel oil for cooling. The combustion chamber wall is set as a heat protection wall structure. Layer 1, foam layer 2 and porous layer 3, one side of foam layer 2 is provided with fuel inlet 4, and fuel inlet 4 is connected with external fuel tank 6 through fuel pipeline 5; 6 enters the foam layer 2 through the fuel pipeline 5, and under the capillary force of the two porous structures of the foam layer 2 and the porous layer 3, the fuel oil 13 is in the porous layer 3 and the inner wall of the combustion chamber, that is, the inner surface of the porous layer 3 Perform strong convective heat exchange and vaporization, absorb a large amount of heat, and can effectively reduce the temperature of the combustion chamber wall. The fuel vapor formed by vaporization during heat exchange forms a thin film boundary layer on the inne...
PUM
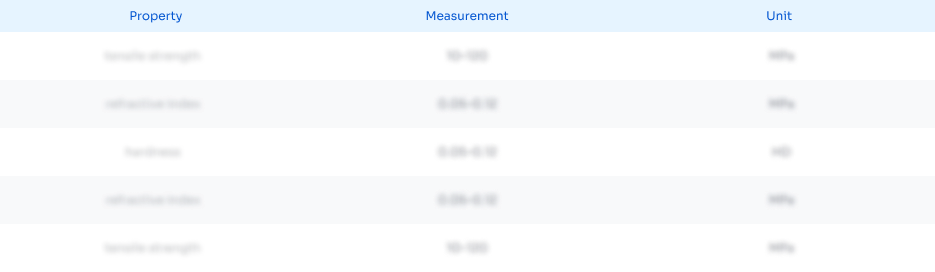
Abstract
Description
Claims
Application Information

- R&D
- Intellectual Property
- Life Sciences
- Materials
- Tech Scout
- Unparalleled Data Quality
- Higher Quality Content
- 60% Fewer Hallucinations
Browse by: Latest US Patents, China's latest patents, Technical Efficacy Thesaurus, Application Domain, Technology Topic, Popular Technical Reports.
© 2025 PatSnap. All rights reserved.Legal|Privacy policy|Modern Slavery Act Transparency Statement|Sitemap|About US| Contact US: help@patsnap.com