Rigid-flexible coupling clamping device
A rigid-flexible coupling, gripper technology, applied in the direction of chucks, manufacturing tools, manipulators, etc., can solve the problems of unfavorable industrial applications, fragile objects, and high costs, to enhance versatility and practicability, and increase load capacity. , the effect of reducing friction
- Summary
- Abstract
- Description
- Claims
- Application Information
AI Technical Summary
Problems solved by technology
Method used
Image
Examples
Embodiment
[0034] Such as Figure 1 to Figure 5 As shown, the rigid-flexible coupling clamper of the present invention includes a clamping mechanism and a driving mechanism, wherein the clamping mechanism includes two clamping parts arranged in a symmetrical mirror image, and a fixed part 6 connected to the two clamping parts, Both clamping parts include a flexible clamping rod one 2 and a flexible clamping rod two 1, the flexible clamping rod one 2 is used as the lower clamping part of the clamping part, and the flexible clamping rod two 1 is used as the upper clamping part of the clamping part The holder realizes the flexible clamping of the clamping object 25. One end of the flexible clamping rod one 2 is connected to the fixing part 6 , and the other end is connected to the flexible clamping rod two 1 . The clamping portion also includes a rigid clamping rod 3 and a rigid clamping drive rod 4 for increasing the load capacity of the clamp, the rigid clamping rod 3 is hinged with the ...
PUM
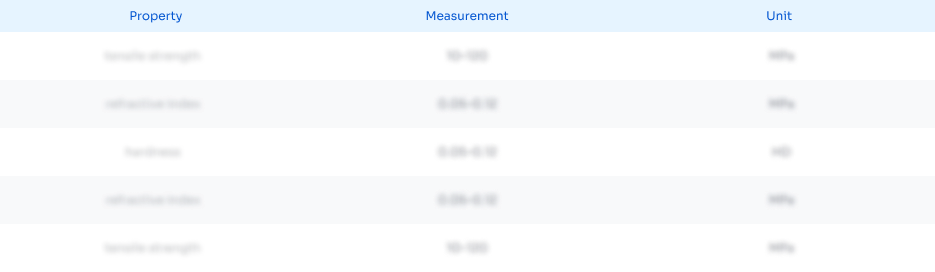
Abstract
Description
Claims
Application Information

- R&D
- Intellectual Property
- Life Sciences
- Materials
- Tech Scout
- Unparalleled Data Quality
- Higher Quality Content
- 60% Fewer Hallucinations
Browse by: Latest US Patents, China's latest patents, Technical Efficacy Thesaurus, Application Domain, Technology Topic, Popular Technical Reports.
© 2025 PatSnap. All rights reserved.Legal|Privacy policy|Modern Slavery Act Transparency Statement|Sitemap|About US| Contact US: help@patsnap.com