An Automatic Trimming Method for 3D Whole Machine Numerical Simulation
A numerical simulation and full-machine technology, which is applied in the field of automatic trim of three-dimensional full-machine numerical simulation, can solve problems such as the absence of full-machine automatic trim technology
- Summary
- Abstract
- Description
- Claims
- Application Information
AI Technical Summary
Problems solved by technology
Method used
Image
Examples
Embodiment Construction
[0040] The features and performances of the present invention will be further described in detail below in conjunction with the embodiments.
[0041] like figure 1 As shown, an automatic trimming method for three-dimensional full-machine numerical simulation provided by this embodiment includes the following steps:
[0042] S1, generate the original calculation grid of the 3D full machine; such as figure 2 As shown, the original computing grid includes a splicing grid block 10; the original computing grid also includes an external grid of the whole machine, that is, the rest of the grids except the splicing grid block 10 are all external grids of the whole machine; The splicing grid block 10 is spliced with the external grid of the whole machine in a splicing manner, and the external grid of the whole machine can be determined by the user, which is not limited in the present invention.
[0043] As a preference in this embodiment, as image 3 As shown, the splicing grid b...
PUM
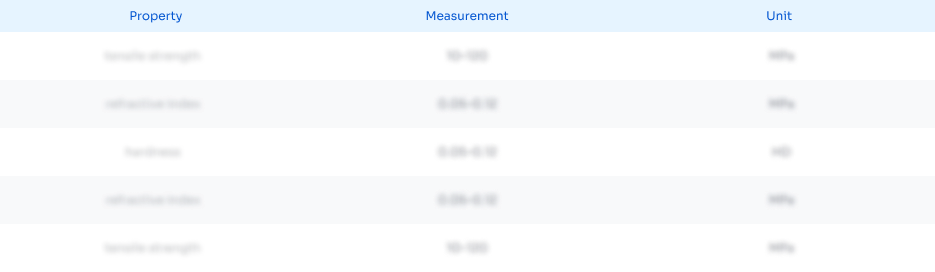
Abstract
Description
Claims
Application Information

- R&D
- Intellectual Property
- Life Sciences
- Materials
- Tech Scout
- Unparalleled Data Quality
- Higher Quality Content
- 60% Fewer Hallucinations
Browse by: Latest US Patents, China's latest patents, Technical Efficacy Thesaurus, Application Domain, Technology Topic, Popular Technical Reports.
© 2025 PatSnap. All rights reserved.Legal|Privacy policy|Modern Slavery Act Transparency Statement|Sitemap|About US| Contact US: help@patsnap.com