Large-modulus straight toothed spur gear precision forging cold-finish forming method for helicopter and die thereof
A spur gear and precision forging technology, which is applied in the manufacture of tools, wheels, forging/pressing/hammer devices, etc., can solve the problems of low die life, poor tooth surface quality, and low tooth profile accuracy, and improve gear performance and service life, improve tooth shape accuracy and surface quality, and improve the effect of forging accuracy
- Summary
- Abstract
- Description
- Claims
- Application Information
AI Technical Summary
Problems solved by technology
Method used
Image
Examples
specific Embodiment approach 1
[0014] Embodiment 1: In this embodiment, a method for precision forging and cold-finishing of large-modulus spur gears for helicopters is specifically carried out according to the following steps:
[0015] 1. Gear blank preparation: According to the design requirements of gear parts, blanking is carried out, and the center split hole is prefabricated in the center of the blank according to the size of the part to obtain the gear blank;
[0016] 2. Cold finishing: use cold finishing to reduce and extrude the tooth blank to obtain the tooth blank after cold finishing;
[0017] 3. End face trimming: remove the burrs on the end face of the tooth blank after cold finishing.
[0018] This embodiment improves the tooth shape precision and tooth surface quality of the forged gear, reduces the forming load, and realizes near-net shaping of the spur gear with large modulus. The forged gear is trimmed by cold finishing, which reduces the subsequent cutting process of the gear surface an...
specific Embodiment approach 2
[0021] Embodiment 2: The difference between this embodiment and Embodiment 1 is that the diameter of the central distribution hole in Step 1 is 45mm. Others are the same as the first embodiment.
specific Embodiment approach 3
[0022] Specific embodiment three: the mold of the precision forging cold finishing forming method of large modulus spur gears for helicopters in this embodiment includes a pre-tightening die device and a punch device; the pre-tightening die device consists of die 5, pre-tightening die device Ring 4, lower backing plate 3 and die fixing ring 15, the interference fit between die 5 and pre-tightening ring 4, the die 5, pre-tightening ring 4, lower backing plate are connected by die fixing ring 15 and bolts 3 is connected with the lower template 1; the punch device is composed of a punch 11, a toothed mandrel 12, a punch fixing plate 7, an upper backing plate 10 and an upper template 6, and the punch 11 is a toothed punch, and the teeth are connected by bolts Shaped mandrel 12, punch 11, upper backing plate 10, punch fixing plate 7 are connected with upper template 6 to ensure that toothed mandrel 12 tooth tops correspond to punch 11 tooth roots, and toothed mandrel 12 tooth roots ...
PUM
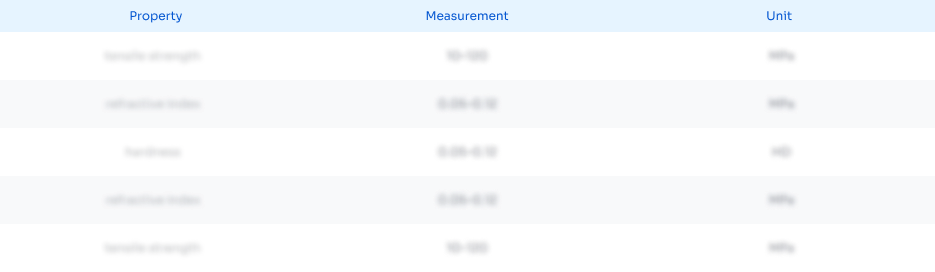
Abstract
Description
Claims
Application Information

- R&D
- Intellectual Property
- Life Sciences
- Materials
- Tech Scout
- Unparalleled Data Quality
- Higher Quality Content
- 60% Fewer Hallucinations
Browse by: Latest US Patents, China's latest patents, Technical Efficacy Thesaurus, Application Domain, Technology Topic, Popular Technical Reports.
© 2025 PatSnap. All rights reserved.Legal|Privacy policy|Modern Slavery Act Transparency Statement|Sitemap|About US| Contact US: help@patsnap.com