Microbial degumming process of linen fiber
A flax fiber and microorganism technology, applied in the direction of bacterial retting, can solve the problems of long degumming cycle, large water consumption, pollution, etc., and achieve the effect of short degumming cycle, reducing pollution and reducing cost.
- Summary
- Abstract
- Description
- Claims
- Application Information
AI Technical Summary
Problems solved by technology
Method used
Examples
Embodiment 1
[0025] A flax fiber microbial degumming process, comprising the following steps:
[0026] (1) Bacterial liquid preparation: transfer the selected bacillus into the strain culture tank, and continue to cultivate at 50°C for one week, and the obtained bacterial liquid has a mass percentage concentration of 35% for later use;
[0027] (2) Wash the flax fiber with 50°C water for 15 minutes before putting it into the float tank, put the washed flax fiber into the float tank, and fill each tank with 500 kg of flax fiber;
[0028] (3) Pour the bacterial liquid into the float tank according to the bath ratio of 1:8, control the pH in the tank at 8.5, the temperature at 50°C, and keep warm for 50 minutes;
[0029] (4) At the end of the heat preservation, the bacterial liquid is recovered into the strain culture tank;
[0030] (5) Configure the pickling solution in the auxiliary vat, add 6 cubic meters of water to the auxiliary vat according to the scale of 165CM, add 4 kg of sulfuric ...
Embodiment 2
[0036] A flax fiber microbial degumming process, comprising the following steps:
[0037] (1) Bacterial liquid preparation: transfer the selected bacillus into the strain culture tank, and continue to cultivate at 48°C for one week, and the obtained bacterial liquid has a mass percentage concentration of 35% for later use;
[0038] (2) Wash the flax fiber with 45°C water for 18 minutes before putting it into the float tank, put the washed flax fiber into the float tank, and fill each tank with 490 kg of flax fiber;
[0039] (3) Pour the bacterial solution into the float tank according to the bath ratio of 1:7.5, control the pH in the tank to 8, and keep the temperature at 55°C for 45 minutes;
[0040] (4) At the end of the heat preservation, the bacterial liquid is recovered into the strain culture tank;
[0041] (5) Configure the pickling solution in the auxiliary tank, add 5 cubic meters of water to the auxiliary tank according to the scale of 165CM, add 3 kg of sulfuric ac...
Embodiment 3
[0047] A flax fiber microbial degumming process, comprising the following steps:
[0048] (1) Bacterial solution preparation: transfer the selected bacillus into the strain culture tank, and continue to cultivate at 52°C for one week, and the obtained bacterial solution has a mass percentage concentration of 40% for later use;
[0049] (2) Wash the flax fiber with 55°C water for 12 minutes before putting it into the float tank, put the washed flax fiber into the float tank, and fill each tank with 510 kg of flax fiber;
[0050] (3) Pour the bacterial solution into the float tank according to the bath ratio of 1:8.5, control the pH in the tank to 9, temperature 45°C, and keep warm for 55 minutes;
[0051] (4) At the end of the heat preservation, the bacterial liquid is recovered into the strain culture tank;
[0052] (5) Configure the pickling solution in the auxiliary tank, add 7 cubic meters of water to the auxiliary tank according to the scale of 165CM, add 5 kg of sulfuric...
PUM
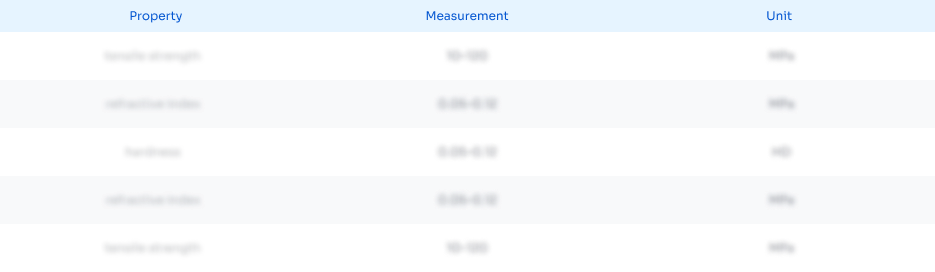
Abstract
Description
Claims
Application Information

- Generate Ideas
- Intellectual Property
- Life Sciences
- Materials
- Tech Scout
- Unparalleled Data Quality
- Higher Quality Content
- 60% Fewer Hallucinations
Browse by: Latest US Patents, China's latest patents, Technical Efficacy Thesaurus, Application Domain, Technology Topic, Popular Technical Reports.
© 2025 PatSnap. All rights reserved.Legal|Privacy policy|Modern Slavery Act Transparency Statement|Sitemap|About US| Contact US: help@patsnap.com