Magnetometer calibration method based on particle swarm optimization of double-objective function
A particle swarm optimization and correction method technology, applied in the field of sensor calibration, which can solve the problems of complex operation, neglect of three-axis magnetic field component constraints, and many sampling points.
- Summary
- Abstract
- Description
- Claims
- Application Information
AI Technical Summary
Problems solved by technology
Method used
Image
Examples
Embodiment Construction
[0072] The present invention will be further described in detail below in conjunction with the accompanying drawings and specific embodiments.
[0073] The purpose of the present invention is to increase the accuracy of parameter estimation and reduce the burden on the computer. The present invention adds an objective function to constrain the magnetic field component in the traditional particle swarm algorithm, and proposes a dual objective function particle based on von Neumann topology. The group optimization algorithm (dual objective Von-PSO) realizes the calibration of the magnetometer. Using a gyroscope as an auxiliary device, an objective function that constrains the three-axis components of the magnetic field is added, and a von Neumann topology is adopted, while the influence of the gyroscope error on the algorithm accuracy is considered. It is proved by theoretical simulation and actual measurement data that the algorithm provided by the invention can guarantee the a...
PUM
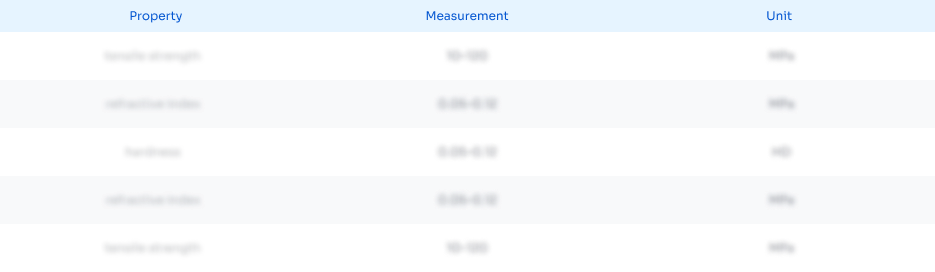
Abstract
Description
Claims
Application Information

- R&D
- Intellectual Property
- Life Sciences
- Materials
- Tech Scout
- Unparalleled Data Quality
- Higher Quality Content
- 60% Fewer Hallucinations
Browse by: Latest US Patents, China's latest patents, Technical Efficacy Thesaurus, Application Domain, Technology Topic, Popular Technical Reports.
© 2025 PatSnap. All rights reserved.Legal|Privacy policy|Modern Slavery Act Transparency Statement|Sitemap|About US| Contact US: help@patsnap.com