Lockable manipulator end executer device capable of realizing constant-force clamping
An end-effector and manipulator technology, applied in manipulators, program-controlled manipulators, chucks, etc., can solve the problems of secondary progressive damage to the operating object, long clamping operation process, complex structure, etc., and achieve high-efficiency and high-reliability picking or packaging. The effect of automatic operation, improved grasping efficiency and flexible movement
- Summary
- Abstract
- Description
- Claims
- Application Information
AI Technical Summary
Problems solved by technology
Method used
Image
Examples
Embodiment Construction
[0008] As shown in Figures 1 and 2, the embodiment of the present invention includes two clamping fingers with different structures: the rotatable finger (1) is connected with one end of the camshaft (3) by a bolt (2), and the camshaft (3) is connected together by a bolt (2). The rotating shaft on one side is connected on the locking member (4), and the pressure spring (11) is connected between the camshaft (3) and the locking member (4), and the locking member (4) is fixed on the frame (7). Slidable finger (10) is connected with slide block (8) by bolt (9), and slide block (8) can slide back and forth on guide rail (14), and guide rail (14) is fixed on the frame (7). The sliding guide post (13) passes through the hole at the top of the slider (8), and the two ends are fixedly connected with the camshaft (3) and the frame (7) respectively, and the return spring (12) is sleeved on the surface of the sliding guide post (13) . The device adopts a manual traction rope (6) to draw...
PUM
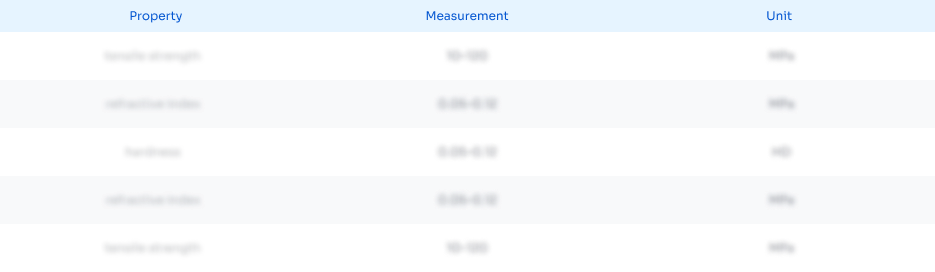
Abstract
Description
Claims
Application Information

- Generate Ideas
- Intellectual Property
- Life Sciences
- Materials
- Tech Scout
- Unparalleled Data Quality
- Higher Quality Content
- 60% Fewer Hallucinations
Browse by: Latest US Patents, China's latest patents, Technical Efficacy Thesaurus, Application Domain, Technology Topic, Popular Technical Reports.
© 2025 PatSnap. All rights reserved.Legal|Privacy policy|Modern Slavery Act Transparency Statement|Sitemap|About US| Contact US: help@patsnap.com