Connector Plating Process
An electroplating process and connector technology, which is applied in the field of connector electroplating technology, can solve problems such as impedance and solder functional hazards, short circuits, etc., and achieve good degreasing effect, flat coating, flat and dense crystal lattice.
- Summary
- Abstract
- Description
- Claims
- Application Information
AI Technical Summary
Problems solved by technology
Method used
Image
Examples
Embodiment approach 1
[0023] This embodiment provides a connector electroplating process, the flow of the process is as follows figure 1 As shown, first place the connector to be plated in the electroplating tank, and then degrease it. The process of degreasing is as follows:
[0024] Keep the temperature of the bath at 60°C, first perform ultrasonic degreasing on the connectors to be plated for 5-10 seconds, and then keep the current density at 12-18ASD (at this time, the temperature of the bath is still 60°C) and perform cathodic electrolytic degreasing on them (connectors to be plated Connect the plug-in to the cathode) for 10-20 seconds, and finally keep the current density at 12-18ASD (at this time, the temperature of the bath is still 60°C) for anodic electrolytic degreasing (the connector to be plated is connected to the anode) for 5-10 seconds; After two washes at room temperature, wash again in hot water at a temperature of 45-55°C.
[0025] After degreasing and water washing, carry out p...
Embodiment approach 2
[0035] This embodiment provides a connector electroplating process, the degreasing process is exactly the same as Embodiment 1; in the pickling activation process, after uniform mixing of 30% ammonium bifluoride and 70% sodium fluoride, the mixture is weighed to prepare 80 g / L Aqueous solution, energized voltage is 4V, all the other are identical with embodiment 1; In the nickel plating process, when nickel-phosphorus-tellurium multi-element alloy nickel is plated for the first time, the mass percentage of phosphorus wherein is 0.2%, the mass percentage of tellurium 0.2%, the second When nickel-phosphorus-tellurium multi-element alloy nickel is plated for the second time, the mass percentage of phosphorus and tellurium is 0.2% and 0.2% by mass.
Embodiment approach 3
[0037] This embodiment provides a connector electroplating process, the degreasing process is exactly the same as Embodiment 1; in the pickling activation process, after uniform mixing of 30% ammonium bifluoride and 70% sodium fluoride, the mixture is weighed to prepare 100 g / L Aqueous solution, energized voltage is 4V, all the other are identical with embodiment 1; In the nickel plating process, when nickel-phosphorus-tellurium multi-element alloy nickel is plated for the first time, the mass percentage of phosphorus wherein is 0.1%, the mass percentage of tellurium 0.1%, the second When nickel-phosphorus-tellurium multi-element alloy nickel is plated for the second time, the mass percentage of phosphorus and tellurium is 0.1% and 0.1% by mass.
PUM
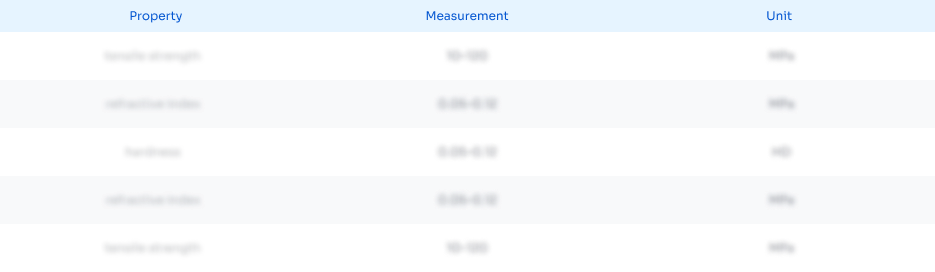
Abstract
Description
Claims
Application Information

- R&D
- Intellectual Property
- Life Sciences
- Materials
- Tech Scout
- Unparalleled Data Quality
- Higher Quality Content
- 60% Fewer Hallucinations
Browse by: Latest US Patents, China's latest patents, Technical Efficacy Thesaurus, Application Domain, Technology Topic, Popular Technical Reports.
© 2025 PatSnap. All rights reserved.Legal|Privacy policy|Modern Slavery Act Transparency Statement|Sitemap|About US| Contact US: help@patsnap.com