Ground zero-gravity debugging device for space rotating mechanism
A space rotation, zero-gravity technology, applied in the field of space rotation mechanism debugging devices, can solve the problems affecting the service life of the shaft system and aggravating bearing wear, and achieve the effects of long-life use, prevention of wear risks, and stable hoisting.
- Summary
- Abstract
- Description
- Claims
- Application Information
AI Technical Summary
Problems solved by technology
Method used
Image
Examples
Embodiment Construction
[0021] The content of the present invention will be further described in detail below in conjunction with the accompanying drawings and specific embodiments.
[0022] In the actual working condition of the space rotation mechanism on the rail, the preload force of the bearing is required to be as small as possible, so as to obtain a lower friction torque, which is beneficial to long-life use. However, in the process of ground debugging, a larger preload is required to ensure that the shafting meets the load-bearing requirements under the action of gravity and no unloading occurs. In order to avoid the contradiction between the two, the present invention provides a zero-gravity debugging device on the ground of the space rotation mechanism, which ensures that the bearing condition of the shaft system is guaranteed as much as possible during the ground debugging process of the space rotation mechanism before launch, and prevents excessive use Potential risk of wear and tear, thu...
PUM
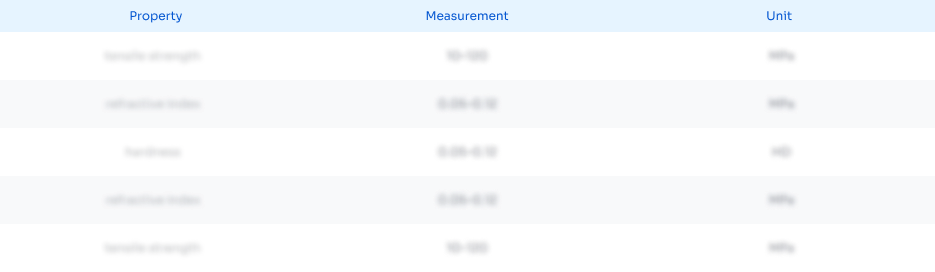
Abstract
Description
Claims
Application Information

- R&D
- Intellectual Property
- Life Sciences
- Materials
- Tech Scout
- Unparalleled Data Quality
- Higher Quality Content
- 60% Fewer Hallucinations
Browse by: Latest US Patents, China's latest patents, Technical Efficacy Thesaurus, Application Domain, Technology Topic, Popular Technical Reports.
© 2025 PatSnap. All rights reserved.Legal|Privacy policy|Modern Slavery Act Transparency Statement|Sitemap|About US| Contact US: help@patsnap.com