A kind of workpiece dislocation grasping method
A workpiece, reverse direction technology, applied in the direction of unstacking of objects, conveyor objects, transportation and packaging, etc., can solve the problem that the workpiece cannot complete the automatic grabbing operation, and achieve the effect of automatic control
- Summary
- Abstract
- Description
- Claims
- Application Information
AI Technical Summary
Problems solved by technology
Method used
Image
Examples
Embodiment 1
[0034]According to the shape of the workpiece, there are single-sided types. When the workpieces are stacked in front and back order, the center axis of the workpiece does not overlap with the center axis of the entire stack of workpieces. The workpiece in the above-mentioned stacking method cannot be automatically grasped.
[0035]Such asfigure 1 As shown, in order to solve the above problem, this embodiment proposes a workpiece dislocation grasping method, which is used for the case where the central axis of the workpiece does not overlap with the central axis of the entire stack of workpieces, and the hardware includes at least two sets of initial positions for the entire stack of workpieces. The central axis is the clamping jaws symmetrically arranged along the axis of the axis.
[0036]The workpieces are mostly made of plates with two supporting legs. In this embodiment, the side where the supporting legs are located is the length direction, and the width direction is perpendicular t...
Embodiment 2
[0070]Based on the workpiece dislocation grabbing method described in Embodiment 1, this embodiment provides a workpiece grabbing device, which is used to grab a workpiece that is overlapped left and right.
[0071]Such asFigure 2-3As shown, in addition to the two sets of linked clamping jaws 100 required in the workpiece dislocation grasping method, the hardware structure also includes a workpiece detection assembly 200 located at one of the clamping jaws 100 and a movement distance detection assembly.
[0072]The workpiece detection assembly 200 moves synchronously with the gripper 100, and generates a trigger signal when the gripper 100 reaches the side of the topmost workpiece;
[0073]The movement distance detection component acquires the movement distance of the gripper 100 during the process from the start of the workpiece detection component 200 to the generation of the trigger signal;
[0074]Two sets of clamping jaws 100 are located above the entire stack of workpieces, and their init...
Embodiment 3
[0089]This embodiment provides a workpiece grasping device, which is used to grasp a workpiece that is overlapped left and right.
[0090]It also includes two sets of linked clamping jaws 100, a workpiece detection assembly 200 located at one of the clamping jaws 100, and a movement distance detection assembly.
[0091]The workpiece detection assembly 200 moves synchronously with the gripper 100, and generates a trigger signal when the gripper 100 reaches the side of the topmost workpiece; moves the distance detection module, and acquires that the workpiece detection module 200 starts to generate the trigger signal. Movement distance; two sets of grippers 100 are located above the entire stack of workpieces, and the initial position is symmetrically set along the width direction of the workpiece with the center axis of the entire stack of workpieces, and moves to the topmost workpiece according to the movement distance obtained by the moving distance detection assembly Right above, and mo...
PUM
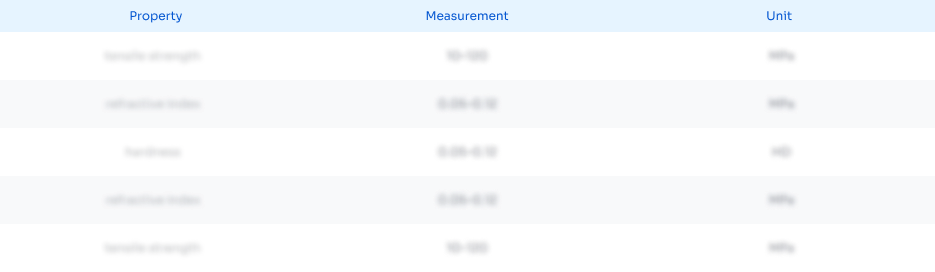
Abstract
Description
Claims
Application Information

- R&D
- Intellectual Property
- Life Sciences
- Materials
- Tech Scout
- Unparalleled Data Quality
- Higher Quality Content
- 60% Fewer Hallucinations
Browse by: Latest US Patents, China's latest patents, Technical Efficacy Thesaurus, Application Domain, Technology Topic, Popular Technical Reports.
© 2025 PatSnap. All rights reserved.Legal|Privacy policy|Modern Slavery Act Transparency Statement|Sitemap|About US| Contact US: help@patsnap.com