Four-wheel driving AGV (Automatic Guided Vehicle) tracking method based on Ackermann steering principle
A principle and corner technology, applied in the field of four-wheel-drive AGV tracking based on the Ackerman steering principle, can solve the problems of cracking on the edge of the roller, unable to meet the power demand, and the problem of driving wheel vibration cannot be well solved, etc. Small track radius, improved reliability and stability, reduced reliance on site openness
- Summary
- Abstract
- Description
- Claims
- Application Information
AI Technical Summary
Problems solved by technology
Method used
Image
Examples
Embodiment Construction
[0027] Such as figure 1 with figure 2 As shown, in the method of the present invention, the AGV drive consists of four groups of steering wheels evenly distributed on the bottom surface of the AGV, and the tracing and traction is completed by three cameras arranged on the bottom surface of the AGV, of which two cameras are arranged on the center line of the forward direction of the AGV , The other is set on the midline of the lateral direction perpendicular to the forward direction of the AGV and deviated from the midline of the forward direction of the AGV. This camera is used for overhead photography of the ribbon when the AGV moves laterally. The principle is the same as the following process. The tracking process of the camera that is set on the midline of the lateral direction perpendicular to the advancing direction of the AGV and deviated from the midline of the advancing direction of the AGV is not described here. The method generally includes the following steps:
[00...
PUM
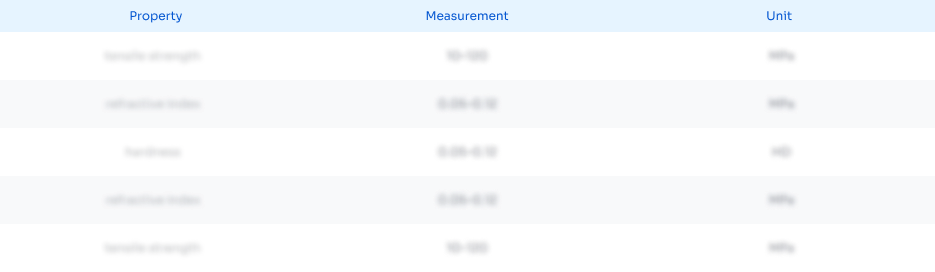
Abstract
Description
Claims
Application Information

- R&D Engineer
- R&D Manager
- IP Professional
- Industry Leading Data Capabilities
- Powerful AI technology
- Patent DNA Extraction
Browse by: Latest US Patents, China's latest patents, Technical Efficacy Thesaurus, Application Domain, Technology Topic, Popular Technical Reports.
© 2024 PatSnap. All rights reserved.Legal|Privacy policy|Modern Slavery Act Transparency Statement|Sitemap|About US| Contact US: help@patsnap.com