Double-robot cooperative working device
A collaborative work, dual-robot technology, applied in the fields of instruments, manipulators, manufacturing tools, etc., can solve the problems of complex manipulator control, affecting the efficiency of teaching, and troublesome operation.
- Summary
- Abstract
- Description
- Claims
- Application Information
AI Technical Summary
Problems solved by technology
Method used
Image
Examples
Embodiment 1
[0025] see Figure 1 to Figure 5 , the figure shows a dual-robot cooperative working device provided by Embodiment 1 of the present invention, which includes a first robotic arm 1 and a second robotic arm 2 oppositely arranged, the first robotic arm 1 is a multi-axis robotic arm, and the second robotic arm The second mechanical arm 2 is a multi-axis mechanical arm, the first mechanical arm 1 is rotatably mounted on the first base 11, and the second mechanical arm 2 is rotatably mounted on the second base 21; as an improvement, the first mechanical arm 1 A drive motor 13 is installed on the first operating end 12 of the drive motor 13, and a clamp part 14 is connected to the drive shaft of the drive motor 13. The clamp part 14 includes a turntable 141, and a flange 146 is connected to the turntable 141, which is connected to the drive of the drive motor 13. On the side edge of the shaft, the turntable 141 is fixedly installed with a plurality of installation substrates 142 unif...
Embodiment 2
[0029] see Figure 1 to Figure 3 , the figure shows a dual-robot cooperative working device provided by the second embodiment of the present invention. On the basis of the above-mentioned embodiment, this embodiment further makes the following technical solutions as improvements: the first mechanical arm 1 and An isolation net 3 is arranged outside the second mechanical arm 2, and the isolation net 3 is a rectangular isolation net when viewed from above. Through the setting of the above structure, the isolation function during operation can be realized.
Embodiment 3
[0031] see Figure 1 to Figure 3 , the figure shows a dual-robot cooperative working device provided by the third embodiment of the present invention. On the basis of the above-mentioned embodiment, this embodiment further makes the following technical solution as an improvement: the outer casing of the turntable 141 is equipped with a ring Shaped body 144, the inner wall of the annular body 144 is circular, the outer wall of the annular body 144 is polygonal, the mounting substrate 142 is detachably connected to the plane 145 of the annular body 144, and the mounting substrate 142 is a rectangular plate. Through the setting of the above structure, the setting of the plane can ensure the stability of the tool installation, and the polygonal annular body can reduce the wind resistance during rotation, that is, the wind direction will be tangent to the turntable due to the guidance of the plane, so that when working, the rotation of the turntable The rotation resistance will be ...
PUM
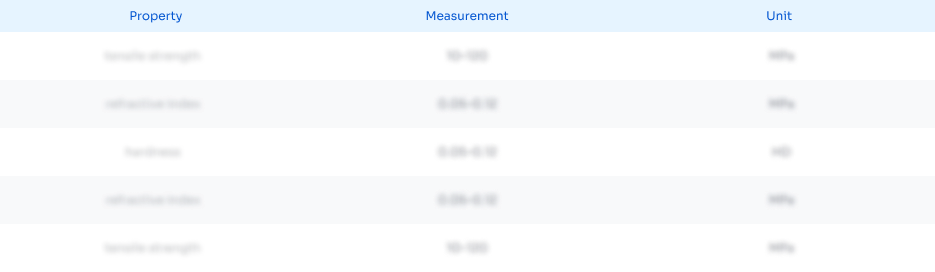
Abstract
Description
Claims
Application Information

- R&D
- Intellectual Property
- Life Sciences
- Materials
- Tech Scout
- Unparalleled Data Quality
- Higher Quality Content
- 60% Fewer Hallucinations
Browse by: Latest US Patents, China's latest patents, Technical Efficacy Thesaurus, Application Domain, Technology Topic, Popular Technical Reports.
© 2025 PatSnap. All rights reserved.Legal|Privacy policy|Modern Slavery Act Transparency Statement|Sitemap|About US| Contact US: help@patsnap.com