Engine pre-swirl system
A pre-rotation system and engine technology, applied in engine functions, engine components, machines/engines, etc., can solve the problems of poor cooling effect of airflow channels and difficult manufacturing, avoid flow separation, reduce manufacturing difficulty, reduce The effect of flow loss
- Summary
- Abstract
- Description
- Claims
- Application Information
AI Technical Summary
Problems solved by technology
Method used
Image
Examples
Embodiment 1
[0041] Figure 5 It is a schematic diagram of the first embodiment of the engine pre-swirl system of the present invention after being divided along the circumferential surface of revolution. Image 6 It is an axonometric view of the rotary plane in Embodiment 1 of the engine pre-swirl system of the present invention. Figure 7 It is a forward projection view of the outlet axial section of the rectifying vane in Embodiment 1 of the engine pre-swirl system of the present invention. Figure 8 It is a rear projection view of the axial section at the inlet of the downstream channel in Embodiment 1 of the engine pre-swirl system of the present invention.
[0042] like Figure 5 to Figure 8As shown, the present invention discloses a kind of engine pre-swirl system, the upstream of the pre-swirl nozzle 10 is provided with a plurality of rectifying blades 20, according to the needs of the original through-flow pillar to circulate cold air, the rectifying blades 20 are provided with ...
Embodiment 2
[0048] Figure 9 It is an axonometric view of the rotary plane in Embodiment 2 of the engine pre-swirl system of the present invention. like Figure 9 As shown, the structure of this embodiment is basically the same as that of Embodiment 1, and the difference is that a plurality of vane-shaped nozzle cascades 30 are arranged downstream of the rectifying vane 20 for rectifying the incoming flow, and the rectifying vane 20 and the nozzle The deflection directions of the cascades 30 are the same, and the airflow deflection angle ranges from 0° to 80°. A rectifying vane channel 40 is formed between two adjacent rectifying vanes 20 , and a nozzle channel 50 is formed between two adjacent nozzle cascades 30 . Preferably, the deflection angle of the air flow from the inlet of the rectifying blade 20 to the outlet of the nozzle cascade 30 is in the range of 70°-80°. The direction of the air outlet angle of the rectifying blade 20 deviates from the inlet angle of the blade of the no...
PUM
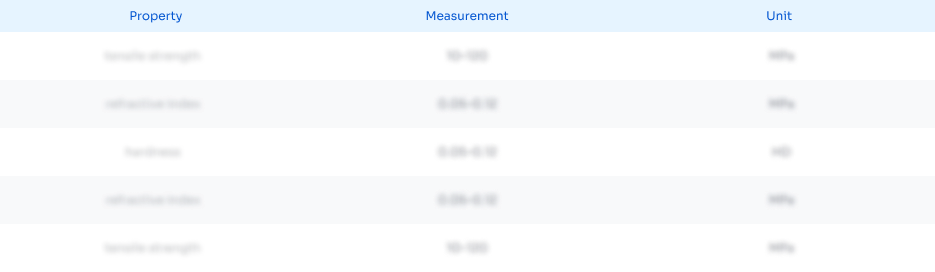
Abstract
Description
Claims
Application Information

- Generate Ideas
- Intellectual Property
- Life Sciences
- Materials
- Tech Scout
- Unparalleled Data Quality
- Higher Quality Content
- 60% Fewer Hallucinations
Browse by: Latest US Patents, China's latest patents, Technical Efficacy Thesaurus, Application Domain, Technology Topic, Popular Technical Reports.
© 2025 PatSnap. All rights reserved.Legal|Privacy policy|Modern Slavery Act Transparency Statement|Sitemap|About US| Contact US: help@patsnap.com