Method and device thereof for shallow type drilling machine self-adaptive balance
An adaptive drilling rig technology, applied in support devices, automatic drilling control systems, earthwork drilling and production, etc., can solve problems such as unsuitable submersible drilling rigs, and achieve easy installation and maintenance, increased support range, and high-speed support positioning Effect
- Summary
- Abstract
- Description
- Claims
- Application Information
AI Technical Summary
Problems solved by technology
Method used
Image
Examples
Embodiment 1
[0041] At first the drilling rig is advanced to the vicinity of the rock wall that needs to be drilled, and then the front support leg (3) and the rear support leg (18) of the initial support device are first supported on the ground. Then use the laser rangefinder (1) and the angular displacement sensor (2) to obtain real-time position information of the drilling face of the tunnel rock wall, for example, the measured distance is 1.5m, and the angle is 20°. The angle value γ can be obtained by the above algorithm is 27.5°. Look up table 3 and know that this angle is less than 30 °, so central controller (17) does not have drive signal output. The hydraulic pump does not work, so the supporting device remains in its original state. At this time, it is in the working state that does not need to start the self-adaptive balancing device.
Embodiment 2
[0043] At first the drilling rig is advanced to the vicinity of the rock wall that needs to be drilled, and then the front support leg (3) and the rear support leg (18) of the initial support device are first supported on the ground. Then use the laser range finder (1) and the angular displacement sensor (2) to obtain real-time position information of the tunnel rock wall drilling face, for example, the measured distance is 2.5m, the angle is 40°, and the angle value γ can be obtained by the above algorithm It is 52.5°, and it can be seen from Table 3 that the angle is in the range of 50°-60°, so there is a drive signal output. Specific steps are as follows:
[0044] (1) The hydraulic pump works, first the central controller (17) drives the deflection oil cylinder (13) to extend 55cm from the extended end;
[0045] (2) After the working stroke of the deflection cylinder ends, the support cylinder (9) starts to work, so that the sawtooth support claw (10) supports the ground. ...
Embodiment 3
[0048] At first the drilling rig is advanced to the vicinity of the rock wall that needs to be drilled, and then the front support leg (3) and the rear support leg (18) of the initial support device are first supported on the ground. Then use the laser range finder (1) and the angular displacement sensor (2) to obtain real-time position information of the tunnel rock wall drilling face, for example, the measured distance is 4m, and the angle is 70°. The angle value γ obtained by the above algorithm is 90°, look up Table 3, it can be seen that the angle is in the range of more than 80°, so there is a drive signal output. The body steps are as follows:
[0049] (1) The hydraulic pump works, so at first the central controller (17) drives the deflection oil cylinder (13) overhanging end 100cm (reaching the maximum working stroke place).
[0050] (2) After the working stroke of the deflection cylinder ends, the support cylinder (9) starts to work, so that the sawtooth support claw...
PUM
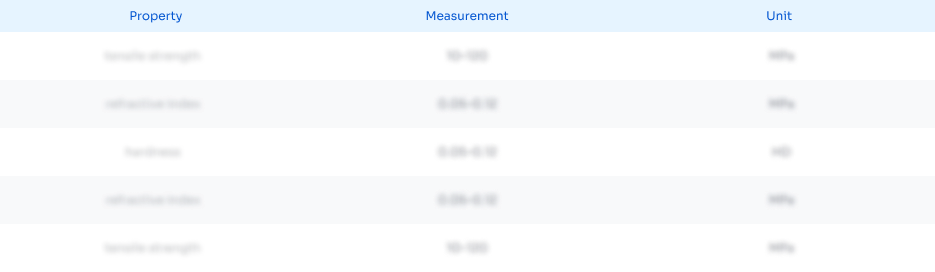
Abstract
Description
Claims
Application Information

- R&D
- Intellectual Property
- Life Sciences
- Materials
- Tech Scout
- Unparalleled Data Quality
- Higher Quality Content
- 60% Fewer Hallucinations
Browse by: Latest US Patents, China's latest patents, Technical Efficacy Thesaurus, Application Domain, Technology Topic, Popular Technical Reports.
© 2025 PatSnap. All rights reserved.Legal|Privacy policy|Modern Slavery Act Transparency Statement|Sitemap|About US| Contact US: help@patsnap.com