Bionic flapping-wing robot driven by flexible piezoelectric fibers
A flexible piezoelectric and robot technology, which is applied in the direction of helicopters, motor vehicles, aircraft, etc., can solve the problems of insufficient flight power, insufficient flight power, and non-reversible movement of flapping-wing robots, so as to reduce energy consumption, improve flight power, and reduce energy consumption. The effect of small flight resistance
- Summary
- Abstract
- Description
- Claims
- Application Information
AI Technical Summary
Problems solved by technology
Method used
Image
Examples
Embodiment Construction
[0030] The present invention will be described in detail below in conjunction with specific embodiments.
[0031] A bionic flapping wing robot driven by flexible piezoelectric fibers, such as figure 1 and figure 2 As shown, it includes a fuselage 1, a drive-amplifying mechanism 2 and wings 3, and the wings 3 are mounted on the fuselage in pairs, and there are two pairs of wings 3 on the fuselage, and each wing includes ribs 301 and fins 302, each drive-amplification mechanism 2 corresponds to a wing 3, the drive-amplification mechanism 2 is located in the fuselage 1, the drive-amplification mechanism 2 includes three stages of series levers, the first stage lever 201 and the second stage of the drive-amplification mechanism The input ends of the first-level levers 202 are respectively provided with respective piezoelectric actuators, the output ends of the first-level levers 201 and the second-level levers 202 are hinged by a flexible hinge 2021, and the hinge point is used ...
PUM
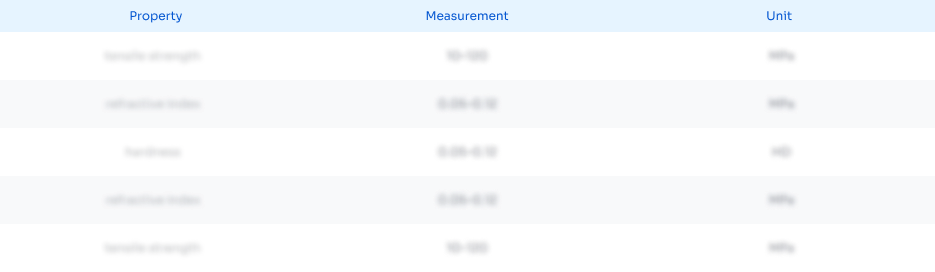
Abstract
Description
Claims
Application Information

- R&D
- Intellectual Property
- Life Sciences
- Materials
- Tech Scout
- Unparalleled Data Quality
- Higher Quality Content
- 60% Fewer Hallucinations
Browse by: Latest US Patents, China's latest patents, Technical Efficacy Thesaurus, Application Domain, Technology Topic, Popular Technical Reports.
© 2025 PatSnap. All rights reserved.Legal|Privacy policy|Modern Slavery Act Transparency Statement|Sitemap|About US| Contact US: help@patsnap.com