Pitot tube device for measuring pressure pulsation of hypersonic wind tunnel
A wind tunnel pressure and hypersonic technology, applied in the field of fluid mechanics, to achieve the effect of solving large errors, improving accuracy, and weakening reflection oscillations
- Summary
- Abstract
- Description
- Claims
- Application Information
AI Technical Summary
Problems solved by technology
Method used
Image
Examples
Embodiment 1
[0029] figure 1 The structural diagram of Example 1 is shown in . The pitot tube device 8 includes a cylindrical body 1 and a sensor 2, and an internally supported connecting piece 3 with the central axis 4 of the cylindrical body and the sensor as the center of rotation. exist figure 1 In Embodiment 1, the cylindrical body includes a front end plane 5, a cylindrical shoulder 6 and a transition fillet 7 therebetween. In this case, the transition radius 7 may be removed or replaced by another aerodynamically suitable contour. Considering the machining problem in Embodiment 1, the main body of the cylindrical shape is divided into two sections at a distance from the front end plane L along the central axis. The length L is affected by the axial length of the sensor and the design of the internally supported connector.
[0030] figure 2 The exploded cross-sectional view of the Pitot tube device is shown. The Pitot tube can alleviate the disturbance reflection problem of the...
Embodiment 2
[0036] Figure 4 Demonstrates different ways to attenuate a pitot tube for ultrasonic measurement of disturbance reflections. In the second embodiment, the pitot tube device is directly composed of the main body 1 and the sensor 2 . The main body 1 formed of a porous metal material can reduce the reflection of disturbances in the supersonic flow field. The positioning connection between the main body 1 and the sensor 2 is completed by the hollow cavity of the main body 1 . The outer profile of the body 1 can be modified to suit the aerodynamic shape. The sensor 2 can be selected from sensors of different models and types.
[0037] Using porous metal materials for pitot tubes to measure pressure fluctuations in hypersonic incoming flow can eliminate part of the influence of incoming flow disturbances. The technical problem is that porous metal materials with different properties, such as permeability, porosity, etc., have great impact on experimental measurements. The corre...
PUM
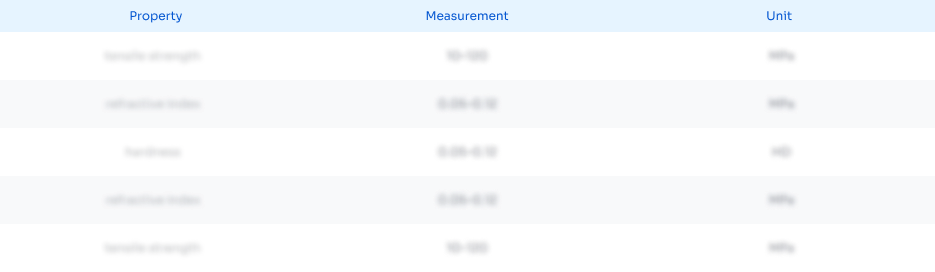
Abstract
Description
Claims
Application Information

- Generate Ideas
- Intellectual Property
- Life Sciences
- Materials
- Tech Scout
- Unparalleled Data Quality
- Higher Quality Content
- 60% Fewer Hallucinations
Browse by: Latest US Patents, China's latest patents, Technical Efficacy Thesaurus, Application Domain, Technology Topic, Popular Technical Reports.
© 2025 PatSnap. All rights reserved.Legal|Privacy policy|Modern Slavery Act Transparency Statement|Sitemap|About US| Contact US: help@patsnap.com