Electric cylinder drive two-translation grabbing robot mechanism of synchronous belt transmission structure
A technology of synchronous belt drive and electric cylinder, which is applied to manipulators, program-controlled manipulators, chucks, etc., can solve the problems of bloated robot structure and large space, and achieve compact overall structure, small space, and kinematics. Good dynamic performance
- Summary
- Abstract
- Description
- Claims
- Application Information
AI Technical Summary
Problems solved by technology
Method used
Image
Examples
Embodiment Construction
[0020] The technical solutions of the present invention will be further described below in conjunction with the accompanying drawings and embodiments.
[0021] control figure 1 , figure 2 , image 3 and Figure 4 , the electric cylinder with synchronous belt transmission structure drives two translational grabbing robot mechanisms, including the frame (1), the first transmission wheel (4), the second transmission wheel (5), the third transmission wheel (8), the fourth transmission wheel Transmission wheel (9), fifth transmission wheel (10), sixth transmission wheel (11), first timing belt (6), second timing belt (7), third timing belt (12), first swing rod (2), the second swing rod (3), the third swing rod (13), the fourth swing rod (14), the first connecting member (15), the second connecting member (16), the connecting rod (18), Moving platform (17), servo motor (19) and electric cylinder (20).
[0022] The first swing link (2) is connected with the frame (1) through t...
PUM
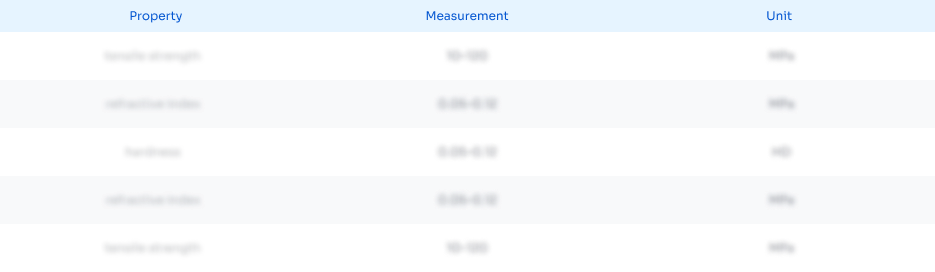
Abstract
Description
Claims
Application Information

- R&D
- Intellectual Property
- Life Sciences
- Materials
- Tech Scout
- Unparalleled Data Quality
- Higher Quality Content
- 60% Fewer Hallucinations
Browse by: Latest US Patents, China's latest patents, Technical Efficacy Thesaurus, Application Domain, Technology Topic, Popular Technical Reports.
© 2025 PatSnap. All rights reserved.Legal|Privacy policy|Modern Slavery Act Transparency Statement|Sitemap|About US| Contact US: help@patsnap.com