Hot-forming line discharging table double-centering system
The technology of centering system and discharging table is applied in the field of double centering system of discharging table of thermoforming line, which can solve the problems of increasing production cost, unable to meet the production of multi-cavity short blanks, reducing production efficiency, etc., and achieves convenient debugging. , Solve the effect of not being able to produce at the same time and having a simple structure
- Summary
- Abstract
- Description
- Claims
- Application Information
AI Technical Summary
Problems solved by technology
Method used
Image
Examples
Embodiment Construction
[0031] The principles and features of the present invention are described below in conjunction with examples, which are only used to explain the present invention and are not intended to limit the scope of the present invention.
[0032] Such as Figure 1-Figure 8 As shown, a double centering system for a thermoforming line discharge table includes a plurality of first centering fingers 2 and a plurality of second centering fingers 3 arranged on the furnace roller frame 1 of the discharge table, and a plurality of the first centering fingers 3 The middle fingers are arranged in a row on the left side of the furnace roll stand, and a plurality of second middle fingers are arranged in a row on the right side of the furnace roll stand, and the first and second middle fingers are respectively arranged on the Between the above-mentioned conveying rollers, a plurality of conveying rollers 4 arranged in parallel are arranged on the furnace roller frame, and the plurality of conveying...
PUM
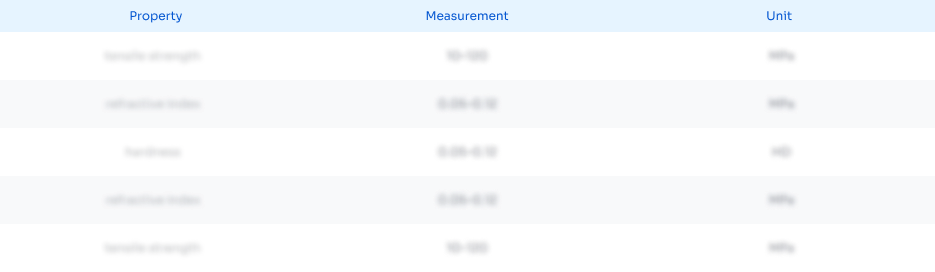
Abstract
Description
Claims
Application Information

- R&D Engineer
- R&D Manager
- IP Professional
- Industry Leading Data Capabilities
- Powerful AI technology
- Patent DNA Extraction
Browse by: Latest US Patents, China's latest patents, Technical Efficacy Thesaurus, Application Domain, Technology Topic, Popular Technical Reports.
© 2024 PatSnap. All rights reserved.Legal|Privacy policy|Modern Slavery Act Transparency Statement|Sitemap|About US| Contact US: help@patsnap.com