An AGV station task distribution system and method
A task allocation and station technology, applied in the field of AGV vehicles, can solve the problems of low efficiency and increase the probability of accidents, and achieve the effect of reducing the problem of low efficiency
- Summary
- Abstract
- Description
- Claims
- Application Information
AI Technical Summary
Problems solved by technology
Method used
Image
Examples
no. 1 example
[0046] refer to figure 1 , this embodiment provides an AGV station task assignment system.
[0047] The AGV station task assignment system includes: a station configuration unit and a dispatching unit.
[0048] The site configuration unit configures attributes for the site.
[0049] In this embodiment, the station refers to the location point where the AGV needs to arrive and perform tasks. Generally speaking, the station is a part of the waypoints. Specifically, the AGV is in a To work in the warehouse, it is necessary to plan the movement routes of the AGV vehicles in the warehouse. These movement routes are generally called paths in this field, and the paths generally include way points and path lines, and the two ends of the path lines are path point, for example, the AGV walks from the gate to the storage registration office and then puts the goods into the shelf. This process may include several route lines and several route points, wherein the route points generally i...
no. 2 example
[0057] refer to figure 2 or image 3 , this embodiment provides an AGV station task assignment method, including the system described in the first embodiment.
[0058] It also includes: the dispatching unit receives the task request of the site, acquires the attributes of the site, searches for the site and assigns an AGV to the site to perform tasks.
[0059] The attributes of the site include initial weight, weight increment, weight increment interval, and maximum limit weight. When the site has a task that needs to be performed by the AGV, the site will send a task request to the dispatching unit, and the dispatching unit will receive the task request of the site and obtain the attributes of the site at the same time. In an embodiment, the scheduling unit simultaneously obtains the initial weight, the weight increment, the weight increment interval, and the maximum limit weight of the station; understandably, the The scheduling unit may also only first obtain the attrib...
no. 3 example
[0075] refer to Figure 4 , the embodiment provides an AGV station task assignment method, including the system described in the first embodiment.
[0076] The attributes of the site include an initial weight, a first changed weight, a second changed weight, and a maximum limit weight. When the site has a task that needs to be performed by the AGV, the site will send a task request to the dispatching unit, and the dispatching unit will receive the task request of the site and obtain the attributes of the site at the same time. In an embodiment, the scheduling unit simultaneously obtains the initial weight, the first change value weight, the second change value weight, and the maximum limit weight of the station; it can be understood that the scheduling The unit may also only obtain the attribute of the initial weight of the site first.
[0077] After the dispatching unit acquires the attributes of the site, it starts to search for the AGV for the site to perform tasks at the...
PUM
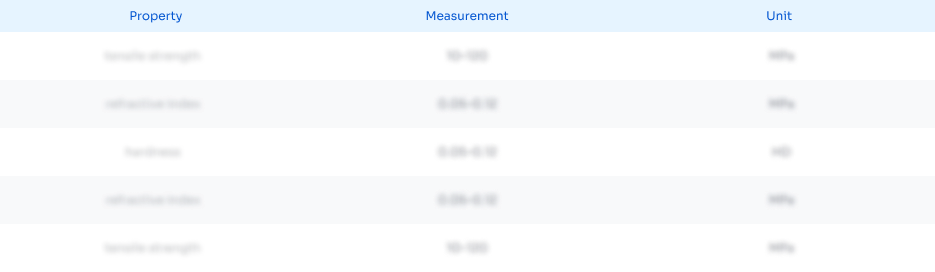
Abstract
Description
Claims
Application Information

- Generate Ideas
- Intellectual Property
- Life Sciences
- Materials
- Tech Scout
- Unparalleled Data Quality
- Higher Quality Content
- 60% Fewer Hallucinations
Browse by: Latest US Patents, China's latest patents, Technical Efficacy Thesaurus, Application Domain, Technology Topic, Popular Technical Reports.
© 2025 PatSnap. All rights reserved.Legal|Privacy policy|Modern Slavery Act Transparency Statement|Sitemap|About US| Contact US: help@patsnap.com