Mechanical compression evaporation and re-dissolution separation nitrate production process
A mechanical compression evaporation, production process technology, applied in the purification of alkali metal sulfite/sulfate, alkali metal chloride, alkali metal halide purification, etc., can solve the problem of shortening the service life of mines or salt lakes and difficult to adapt to the requirements of scientific development , high consumption of raw material brine, etc., to achieve the effect of green production and use of energy, low comprehensive energy consumption and production cost, and safe and reliable process
- Summary
- Abstract
- Description
- Claims
- Application Information
AI Technical Summary
Problems solved by technology
Method used
Image
Examples
Embodiment 1
[0021] 1. Take 100m 3 Sodium sulfate and sodium chloride solution is the raw material solution (Na 2 SO 4 243g / l, NaCl 67g / l), the above raw material solution and 39.1m 3 Heat up salt making mother liquor (Na 2 SO 4 80g / l, NaCl 275g / l) mixed with mechanical compression to evaporate condensed water to preheat to boiling point (boiling point temperature 110°C), enter a section of high-temperature mechanical compression and evaporate to separate and obtain 24.3 tons of solid sodium sulfate (NaCl 2 SO 4 ) and 56.8m 3 A high-temperature nitrate mother liquor (NaCl 307g / l, NaCl 2 SO 4 55g / l);
[0022] 2. 56.8m 3 A high-temperature nitrate mother liquor (NaCl 307g / l, NaCl 2 SO 4 55g / l) into the second-stage high-temperature mechanical compression evaporation (evaporation temperature 100 ° C) to obtain 5.47 tons of sodium chloride (NaCl) and 1.01 tons of sodium sulfate (NaCl) 2 SO 4 ) of solid 39.1m 3 Two-stage high-temperature salt-making nitrate mother liquor (NaCl...
Embodiment 2
[0027] 1. Take 100m 3 Sodium sulfate and sodium chloride solution is the raw material solution (Na 2 SO 4 260g / l, NaCl 50g / l), the above raw material solution and 29.2m 3 Heat up salt making mother liquor (Na 2 SO 4 80g / l, NaCl 275g / l) mixed with mechanical compression to evaporate condensed water to preheat to boiling point (boiling point temperature 110°C), enter a section of high-temperature mechanical compression and evaporate to separate and obtain 26.0 tons of solid sodium sulfate (NaCl 2 SO 4 ) and 42.4m 3 A high-temperature nitrate mother liquor (NaCl307g / l, NaCl 2 SO 4 55g / l);
[0028] 2. 42.4m 3 A high-temperature nitrate mother liquor (NaCl 307g / l, NaCl 2 SO 4 55g / l) into the second-stage high-temperature mechanical compression evaporation (evaporation temperature 100 ° C) to obtain 4.99 tons of sodium chloride (NaCl) and 0.76 tons of sodium sulfate (NaCl) 2 SO 4 ) of solid 29.2m 3 Two-stage high-temperature salt-making nitrate mother liquor (NaCl ...
Embodiment 3
[0033] 1. Take 100m 3 Sodium sulfate and sodium chloride solution is the raw material solution (Na 2 SO 4 210g / l, NaCl 100g / l), the above raw material solution and 58.3m 3 Heat up salt making mother liquor (Na 2 SO 4 80g / l, NaCl 275g / l) mixed with mechanical compression to evaporate condensed water to preheat to boiling point (boiling point temperature 110°C), enter a section of high-temperature mechanical compression and evaporate to separate and obtain 21.0 tons of solid sodium sulfate (NaCl 2 SO 4 ) and 84.8m 3 A high-temperature nitrate mother liquor (NaCl307g / l, NaCl 2 SO 4 55g / l);
[0034] 2. 84.8m 3 A high-temperature nitrate mother liquor (NaCl 307g / l, NaCl 2 SO 4 55g / l) into the second-stage high-temperature mechanical compression evaporation (evaporation temperature 100 ° C) to obtain 8.19 tons of sodium chloride (NaCl) and 4.35 tons of sodium sulfate (NaCl) 2 SO 4 ) of solid 58.3m 3 Two-stage high-temperature salt-making nitrate mother liquor (NaCl...
PUM
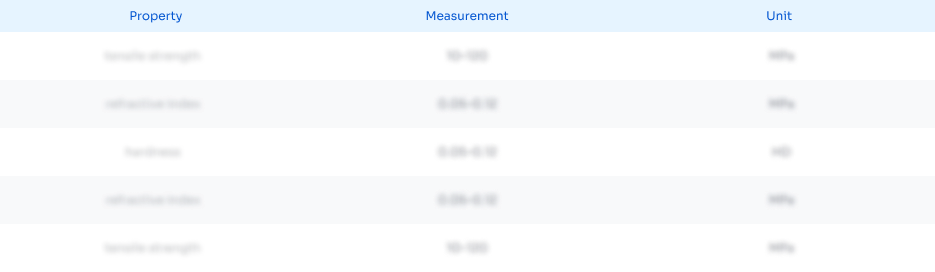
Abstract
Description
Claims
Application Information

- R&D Engineer
- R&D Manager
- IP Professional
- Industry Leading Data Capabilities
- Powerful AI technology
- Patent DNA Extraction
Browse by: Latest US Patents, China's latest patents, Technical Efficacy Thesaurus, Application Domain, Technology Topic, Popular Technical Reports.
© 2024 PatSnap. All rights reserved.Legal|Privacy policy|Modern Slavery Act Transparency Statement|Sitemap|About US| Contact US: help@patsnap.com