Sound producing device and method for manufacturing same
A technology of a sounding device and a manufacturing method, which is applied in the direction of manufacturing tools, laser welding equipment, electrical components, etc., which can solve the problems of small receivers, difficulty in controlling the welding position, and damage to the welding position, so as to reduce the change of impedance and reduce the sound The effect of pulling and suppressing the fluctuation of the magnetic gap
- Summary
- Abstract
- Description
- Claims
- Application Information
AI Technical Summary
Problems solved by technology
Method used
Image
Examples
no. 1 example
[0089] like Figure 7 As shown, in the sounding device 1 as the first embodiment, the fixing portion 32a of the armature 32 and the outer surface 21b of the first yoke 21 are connected by two reference welding portions 51, 51 and two additional welding portions 52, 51 at two positions. 52 to fix the device. The welding part has a total of four positions.
[0090] The plate thicknesses of the first yoke 21 and the second yoke 22 are set to 0.35 mm, and the figure 2The width dimension W1 in the Y direction of the yokes 21 and 22 shown is 1.6 mm, the width dimension W2 in the X direction of the second yoke 22 is 2.7 mm, and the height dimension H in the Z direction of the magnetic field generating unit 20 Set to 1.8mm. As the first magnet 24 and the second magnet, AlNiCo magnets were used. The number of windings of the coil 27 was 200 turns.
[0091] The armature 32 is a PB permalloy, that is, an Fe—Ni alloy containing 45% by mass of Ni, and a thickness of 0.15 mm, figure...
no. 3 example
[0097] like Figure 9 As shown, the sounding device 1 as the third embodiment is formed by welding the fixing portion 32a of the armature 32 and the outer surface 21b of the first yoke 21 with reference welding portions 51 and 51 at two positions and an additional welding portion 52a at six positions in total. , 52a, 52b, 52b and 52c, 52c fixed device. There are eight welding positions in total.
[0098] Other dimensions and the like are the same as in the first embodiment.
[0099] (4) Comparative example
[0100] like Figure 10 As shown, a device in which the fixing portion 32a of the armature 32 and the outer surface 21b of the first yoke 21 are fixed by only two welding portions 53 and 53 is used as a comparative example. The welded portions 53 and 53 are formed at the center position of the first yoke 21 in the Y direction.
[0101] Other dimensions and the like are the same as in the first embodiment.
[0102] (5) Impedance and noise variation
[0103] Figure 1...
PUM
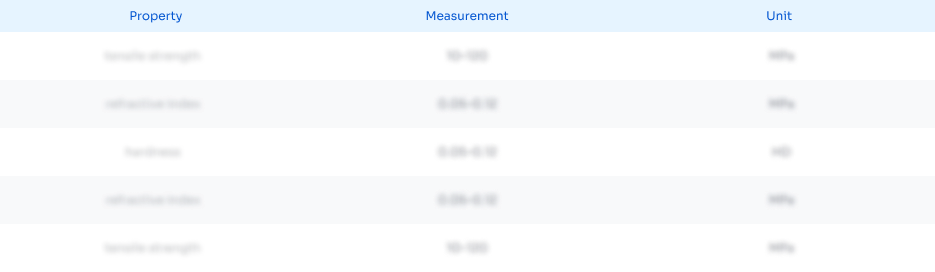
Abstract
Description
Claims
Application Information

- R&D
- Intellectual Property
- Life Sciences
- Materials
- Tech Scout
- Unparalleled Data Quality
- Higher Quality Content
- 60% Fewer Hallucinations
Browse by: Latest US Patents, China's latest patents, Technical Efficacy Thesaurus, Application Domain, Technology Topic, Popular Technical Reports.
© 2025 PatSnap. All rights reserved.Legal|Privacy policy|Modern Slavery Act Transparency Statement|Sitemap|About US| Contact US: help@patsnap.com