Two-stage lossless train capture device for pneumatic damping reduction network train system
A technology of aerodynamic damping and capturing devices, which is applied in railway vehicle testing and other directions, can solve problems such as small scale ratio, high manufacturing precision requirements, and model train track jumping, so as to reduce interaction force, high manufacturing precision requirements, and scale-down smaller than the effect
- Summary
- Abstract
- Description
- Claims
- Application Information
AI Technical Summary
Problems solved by technology
Method used
Image
Examples
Embodiment Construction
[0031] The following is a further description of the technical content of the patent of the present invention, but it is not a limitation to the essential content of the patent of the present invention.
[0032] figure 1 It is a schematic diagram of part of the driving test system on the bridge, including only the test section and the deceleration (train capture) section closely connected with it. During the test, the model train with a certain speed passes through the test section and then enters the deceleration section. The deceleration section is arranged through The two-stage non-destructive capture device of the deceleration net system and the pneumatic damping system realizes the safe and reliable capture of the model train. figure 2 For the overall overview of the deceleration capture segment, image 3 An exploded view of the captured segment for the deceleration, given by figure 2 , 3 It can be seen that the two-stage non-destructive train capture device of the e...
PUM
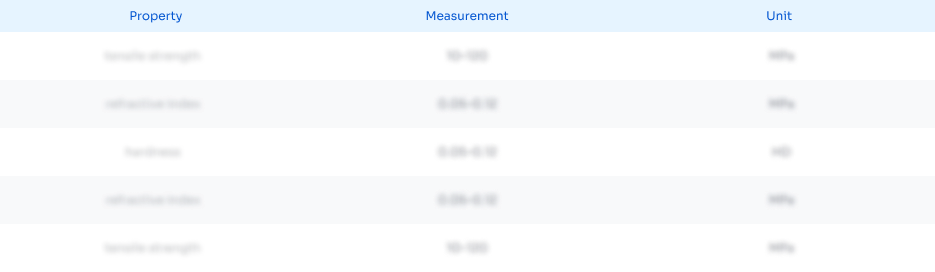
Abstract
Description
Claims
Application Information

- R&D
- Intellectual Property
- Life Sciences
- Materials
- Tech Scout
- Unparalleled Data Quality
- Higher Quality Content
- 60% Fewer Hallucinations
Browse by: Latest US Patents, China's latest patents, Technical Efficacy Thesaurus, Application Domain, Technology Topic, Popular Technical Reports.
© 2025 PatSnap. All rights reserved.Legal|Privacy policy|Modern Slavery Act Transparency Statement|Sitemap|About US| Contact US: help@patsnap.com