Electromechanical servo steering system with spring-loaded bearing arrangement
A technology of steering system and electromechanical servo, which is applied in the direction of electric steering mechanism, portable lifting device, rigid support of bearing components, etc., and can solve problems such as different thermal expansion, tolerance, and increased gap between coupling tooth surfaces
- Summary
- Abstract
- Description
- Claims
- Application Information
AI Technical Summary
Problems solved by technology
Method used
Image
Examples
Embodiment Construction
[0034] exist figure 1 An electromechanical motor vehicle steering system 1 with a steering wheel 2 coupled to an upper steering shaft 3 and a lower steering shaft 4 in a rotationally fixed manner (drehfest) is schematically illustrated in FIG. The upper steering shaft 3 is functionally connected to the lower steering shaft 4 via torsion bars. The lower steering shaft 4 is connected to a pinion 5 in a rotationally fixed manner. The pinion 5 meshes with the toothed section of the toothed rack 6 in the usual manner. The rack 6 is mounted in the steering housing displaceably in the direction of its longitudinal axis. The toothed rack 6 is connected at its free end to the tie rod 7 via a ball joint, not shown. The tie rods 7 are themselves connected in the usual manner via journals to one steered wheel 8 of the motor vehicle, respectively. Rotation of the steering wheel 2 via the connection of the steering shafts 3 , 4 and the pinion 5 causes a longitudinal displacement of the ...
PUM
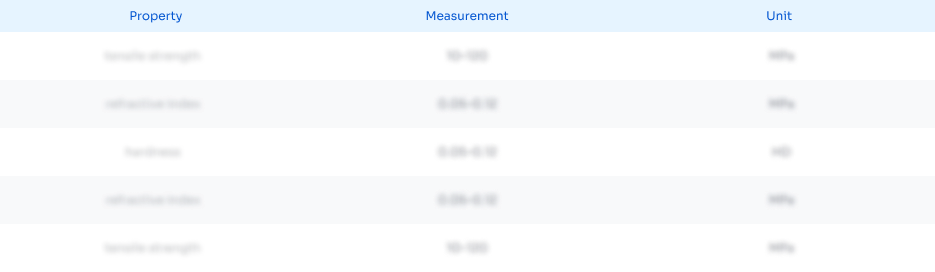
Abstract
Description
Claims
Application Information

- R&D Engineer
- R&D Manager
- IP Professional
- Industry Leading Data Capabilities
- Powerful AI technology
- Patent DNA Extraction
Browse by: Latest US Patents, China's latest patents, Technical Efficacy Thesaurus, Application Domain, Technology Topic, Popular Technical Reports.
© 2024 PatSnap. All rights reserved.Legal|Privacy policy|Modern Slavery Act Transparency Statement|Sitemap|About US| Contact US: help@patsnap.com