Smoothing method of welding robot motion model
A robot movement and welding robot technology, applied in the field of robotics, can solve the problems of fewer algorithms, slow down the convergence speed of algorithms, and the inability to meet the real-time requirements of welding robot motion planning, etc.
- Summary
- Abstract
- Description
- Claims
- Application Information
AI Technical Summary
Problems solved by technology
Method used
Image
Examples
Embodiment Construction
[0066] The present invention is a smoothing method for the motion model of a welding robot. The smoothing method is a non-smooth optimization method proposed based on the non-smooth motion planning model problem of the welding robot. The non-smooth motion planning model problem of the welding robot is a motion planning problem. After mutating the motion planning problem, the non-smooth motion planning model of the welding robot is obtained.
[0067] In this embodiment, first review the welding robot motion planning problem:
[0068] The welding robot is defined as a tree-shaped welding robot with some rigid bodies assembled by joints, that is, the main body is a node and the joints are edges; the motion planning model includes a displacement control variable q(t), which is called a configuration, and the The parameter vector of the joint is the control variable of the motion planning model, and q(t) is abbreviated as q, and the admissible function q needs to satisfy the follow...
PUM
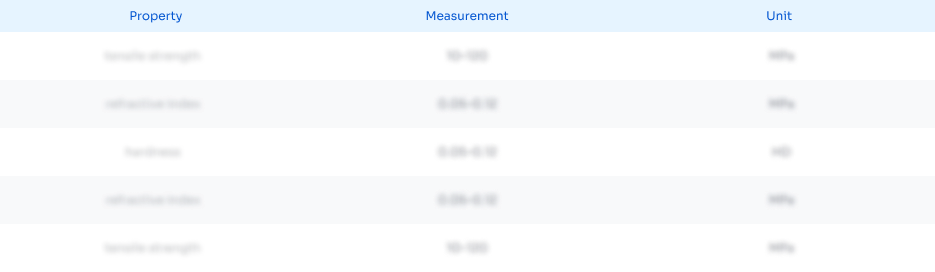
Abstract
Description
Claims
Application Information

- R&D Engineer
- R&D Manager
- IP Professional
- Industry Leading Data Capabilities
- Powerful AI technology
- Patent DNA Extraction
Browse by: Latest US Patents, China's latest patents, Technical Efficacy Thesaurus, Application Domain, Technology Topic, Popular Technical Reports.
© 2024 PatSnap. All rights reserved.Legal|Privacy policy|Modern Slavery Act Transparency Statement|Sitemap|About US| Contact US: help@patsnap.com