Sand-plastic composite material and preparation method thereof
A composite material and sand plastic technology, applied in chemical instruments and methods, separation methods, dispersed particle separation, etc., can solve the problem of less research on purified gas, and achieve the effect of improving contact, increasing the probability of contact, and avoiding agglomeration
- Summary
- Abstract
- Description
- Claims
- Application Information
AI Technical Summary
Problems solved by technology
Method used
Image
Examples
Embodiment 1
[0043] This embodiment provides a method for preparing a sand-plastic composite material, including:
[0044] (1) Negative ion powder and deionized water are mixed according to the mass ratio of 1:10, and the temperature of the water bath is 40° C., and the water bath is ultrasonicated for 10 minutes to obtain the negative ion excitation material slurry;
[0045] (2) Select magnesium-aluminum spinel with a particle size of 2mm, spray aluminum sol on the surface of magnesium-aluminum spinel, so that aluminum sol is evenly coated on the outer surface of magnesium-aluminum spinel, and then spray negative ion excitation material slurry, Dry at 200°C to obtain negative ion generating materials;
[0046] In the negative ion generating material, the mass ratio of magnesium aluminum spinel to negative ion powder is 80:1; the consumption of described aluminum sol is 5% of magnesium aluminum spinel quality;
[0047] (2) Take by weighing 25Kg of quartz sand, 5Kg of negative ion generati...
Embodiment 2
[0054] This embodiment provides a method for preparing a sand-plastic composite material, including:
[0055] (1) Negative ion powder and deionized water are mixed according to the mass ratio of 1:10, and the temperature of the water bath is 40° C., and the water bath is ultrasonicated for 10 minutes to obtain the negative ion excitation material slurry;
[0056] (2) Select magnesium-aluminum spinel with a particle size of 3mm, spray aluminum sol on the surface of magnesium-aluminum spinel, so that aluminum sol is evenly coated on the outer surface of magnesium-aluminum spinel, and then spray negative ion excitation material slurry, Dry at 250°C to obtain negative ion generating materials;
[0057] In the negative ion generating material, the mass ratio of magnesium aluminum spinel to negative ion powder is 80:4; the amount of aluminum sol is 5% of the mass of magnesium aluminum spinel;
[0058] (3) Weigh 35Kg of quartz sand, 7Kg of negative ion generating material, 20Kg of p...
Embodiment 3
[0065] This embodiment provides a method for preparing a sand-plastic composite material, including:
[0066] (1) Mix nano-tourmaline and deionized water according to the mass ratio of 1:10, and at a water bath temperature of 40° C., ultrasonicate the water bath for 10 minutes to obtain a negative ion excitation material slurry;
[0067] (2) Select magnesium-aluminum spinel with a particle size of 5mm, and spray the aluminum sol on the surface of the magnesium-aluminum spinel in a sugar coating machine, so that the aluminum sol is evenly coated on the outer surface of the magnesium-aluminum spinel, and then spray Negative ion excitation material slurry is dried at 300°C to obtain negative ion generating material;
[0068] In the negative ion generating material, the mass ratio of magnesium-aluminum spinel to nano-tourmaline is 100:1; the amount of aluminum sol is 5% of the mass of magnesium-aluminum spinel;
[0069] (3) Weigh 30Kg of quartz sand, 6Kg of negative ion generatin...
PUM
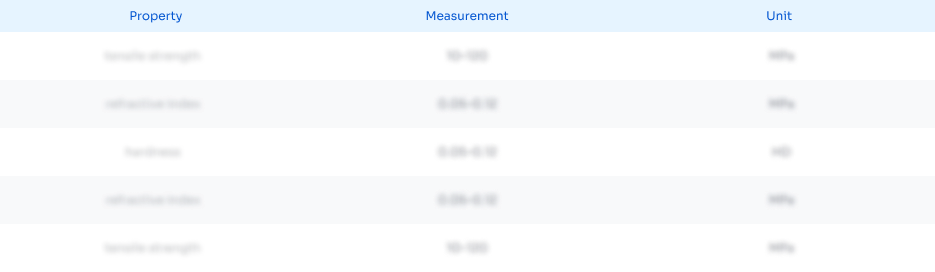
Abstract
Description
Claims
Application Information

- Generate Ideas
- Intellectual Property
- Life Sciences
- Materials
- Tech Scout
- Unparalleled Data Quality
- Higher Quality Content
- 60% Fewer Hallucinations
Browse by: Latest US Patents, China's latest patents, Technical Efficacy Thesaurus, Application Domain, Technology Topic, Popular Technical Reports.
© 2025 PatSnap. All rights reserved.Legal|Privacy policy|Modern Slavery Act Transparency Statement|Sitemap|About US| Contact US: help@patsnap.com