Material distribution device and method
A material distribution and feeding device technology, applied in chemical instruments and methods, mixers with rotary stirring devices, transportation and packaging, etc., can solve the problems of easy stratification, dead ends, and high equipment investment costs, and achieve continuous distribution and mixing , the effect of stable work and simple structure
- Summary
- Abstract
- Description
- Claims
- Application Information
AI Technical Summary
Problems solved by technology
Method used
Image
Examples
Embodiment
[0051] Such as figure 1 As shown, this embodiment provides a material distribution device, including a distributor body 4, a first feeding device and a second feeding device.
[0052] In this embodiment, the distributor body 4 includes a cylinder 401, the upper part of the cylinder 401 is provided with a first feed channel and a second feed channel, the inside of the cylinder 401 is provided with a rotating paddle 409, and the bottom of the cylinder 401 A discharge port 9 is provided. Specifically, the rotating paddle 409 includes a rotating shaft 4091 and blades 4092 , and the blades 4092 are fixed on the rotating shaft 4091 . Preferably, the number of blades 4092 is not less than 3, and the number of blades 4092 is preferably 5, 6, or 7. A supporting structure is provided inside the cylinder 401, and a "U"-shaped or semicircular mounting groove is opened on the supporting structure, and the rotating shaft 4091 of the rotating paddle 409 is installed in the mounting groove....
PUM
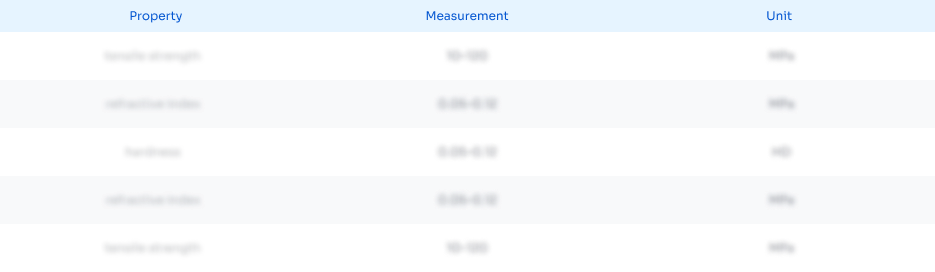
Abstract
Description
Claims
Application Information

- R&D
- Intellectual Property
- Life Sciences
- Materials
- Tech Scout
- Unparalleled Data Quality
- Higher Quality Content
- 60% Fewer Hallucinations
Browse by: Latest US Patents, China's latest patents, Technical Efficacy Thesaurus, Application Domain, Technology Topic, Popular Technical Reports.
© 2025 PatSnap. All rights reserved.Legal|Privacy policy|Modern Slavery Act Transparency Statement|Sitemap|About US| Contact US: help@patsnap.com