Buck-Boost converter variable damping passive control method based on port controlled dissipation Hamiltonian model
A passive control and converter technology, used in control/regulation systems, output power conversion devices, DC power input conversion to DC power output, etc., can solve the problem of slow response speed, small steady-state error, and overshoot Large steady-state error, etc.
- Summary
- Abstract
- Description
- Claims
- Application Information
AI Technical Summary
Problems solved by technology
Method used
Image
Examples
Embodiment Construction
[0084] The present invention will be further described below in conjunction with the accompanying drawings.
[0085] A variable damping passive control method for a Buck-Boost converter based on a port-controlled dissipation Hamiltonian model, comprising the following steps:
[0086] Step 1, according to the system state average model and state variables of the Buck-Boost converter, the system state average model of the Buck-Boost converter is transformed into the port controlled dissipation Hamiltonian model form, and the port controlled dissipation Hamiltonian is verified Passivity of the model, the process is as follows:
[0087] 1.1, the Buck-Boost converter system state average model is expressed in the following form:
[0088]
[0089] Among them, i L is the inductor current, v o is the output voltage, V in is the input voltage, L, C, R are the inductance, capacitance and load resistance of the Buck-Boost converter respectively; u d is the control input;
[0090...
PUM
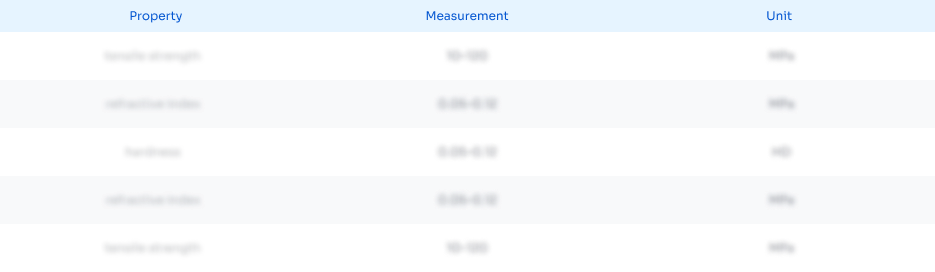
Abstract
Description
Claims
Application Information

- R&D
- Intellectual Property
- Life Sciences
- Materials
- Tech Scout
- Unparalleled Data Quality
- Higher Quality Content
- 60% Fewer Hallucinations
Browse by: Latest US Patents, China's latest patents, Technical Efficacy Thesaurus, Application Domain, Technology Topic, Popular Technical Reports.
© 2025 PatSnap. All rights reserved.Legal|Privacy policy|Modern Slavery Act Transparency Statement|Sitemap|About US| Contact US: help@patsnap.com